Organizations that view quality as the sole responsibility of the “quality controller” or a “quality department” have seen limited success.
Quality permeates an organization from the arrival of raw materials to the departure of finished products. It is ingrained in every step of the process and must be embraced by all.
Since errors have a multiplier effect, failure to meet requirements in one area creates problems elsewhere that have a cascading negative effect across the organization.
What is Total Quality Management
Total Quality Management (TQM) is a process-oriented system, the foundation of which is based on the belief that quality is a matter of conforming to customer’s requirements at every stage. It is both a framework and a philosophy to create conditions for continuous improvement in everything an organization does by leveraging individual effort and extending its effect throughout an organization and beyond.
The International Organization for Standardization (ISO)[1] defines TQM as:
“A management approach for an organization, centered on quality, based on the participation of all its members and aiming at long-term success through customer satisfaction, and benefits to all members of the organization and to society.”
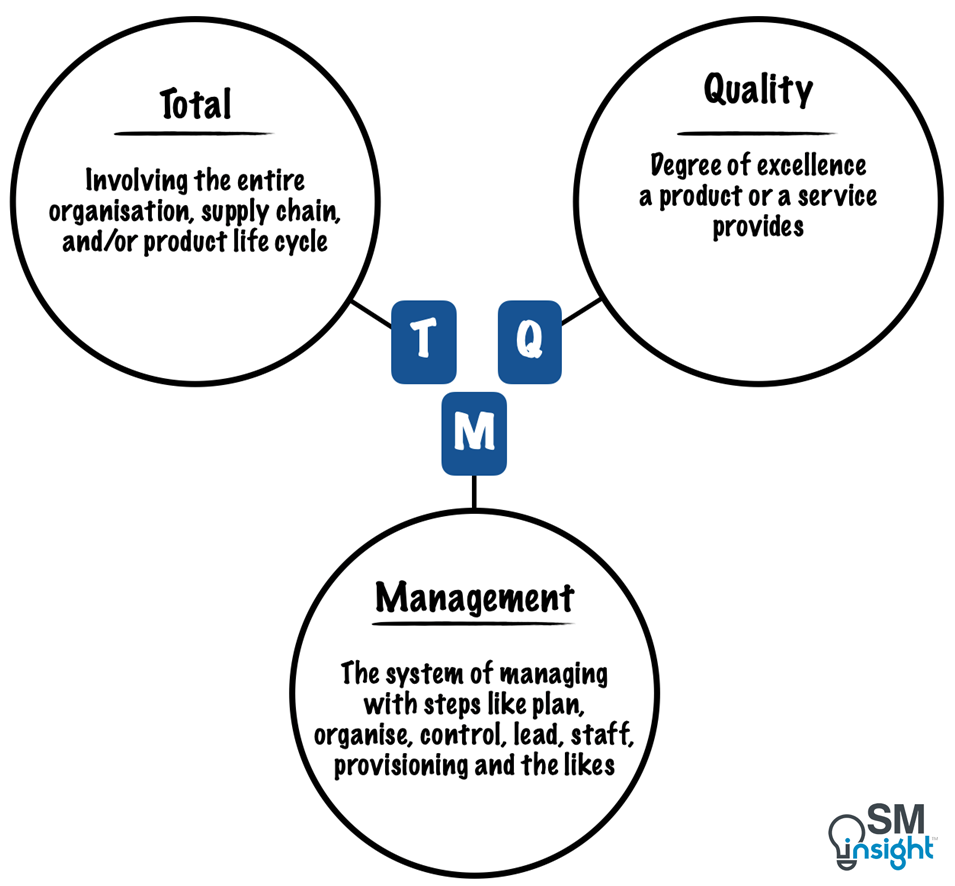
TQM encourages businesses to concentrate on integrated, process-centric quality management, continuous improvements, and fact-based decision-making.
Origin of Total Quality Management
The term TQM is an umbrella methodology drawing on knowledge of the principles and practices of the behavioral sciences, the analysis of quantitative and nonquantitative data, economics theories, and process analysis to continually improve the quality of all processes.
TQM was a natural outgrowth of statistical process control (SPC) and was developed by a number of Japanese firms in the 1950s and 1960s. It was built largely on the teachings of W. Edwards Deming and Joseph Juran, two Americans who had developed the principles in the aftermath of the Second World War.[3]
In the 70s and 80s, the adoption of TQM principles made Japanese companies hugely successful and put them way ahead of their foreign competitors. For example, in 1983, one Harvard study found that the average assembly-line defect rate for a Japanese company was almost 70 times lower than its competitors in the US.[4]
Faced with stiff competition in the 1980s, American businesses began to realize the potential of TQM which led to its widespread adoption by the West.
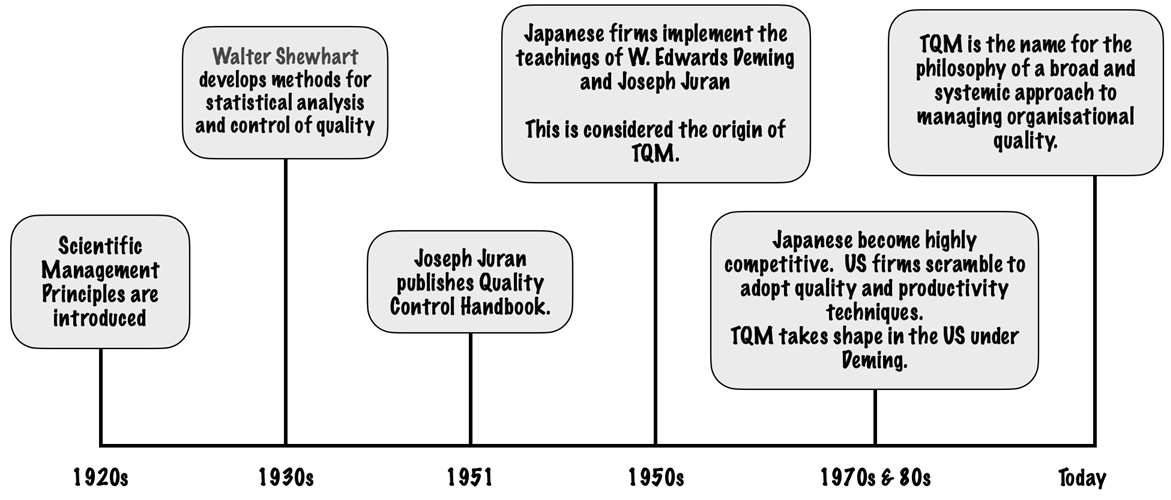
The TQM business approach also formed the basis for the Malcolm Baldrige National Quality Award (MBNQA)[7], an annual award established in 1987 to recognize U.S. organizations for performance excellence under the BPEP criteria.
While there is no widely agreed-upon approach, TQM efforts typically draw heavily on the previously developed tools and techniques of quality control and have enjoyed widespread attention during the late 1980s and early 1990s before being overshadowed by ISO 9000, Lean manufacturing, and Six Sigma.[8]
Eight elements of Total Quality Management
TQM is based on a set of management approaches for a customer-oriented organization that embeds all employees in continuous improvement. It is based on strategy, data, and efficient communication to integrate quality discipline into corporate culture and activities.
While multiple concepts of TQM can be found in modern Quality Management Systems (QMSs), broadly, there are eight elements crucial to it:
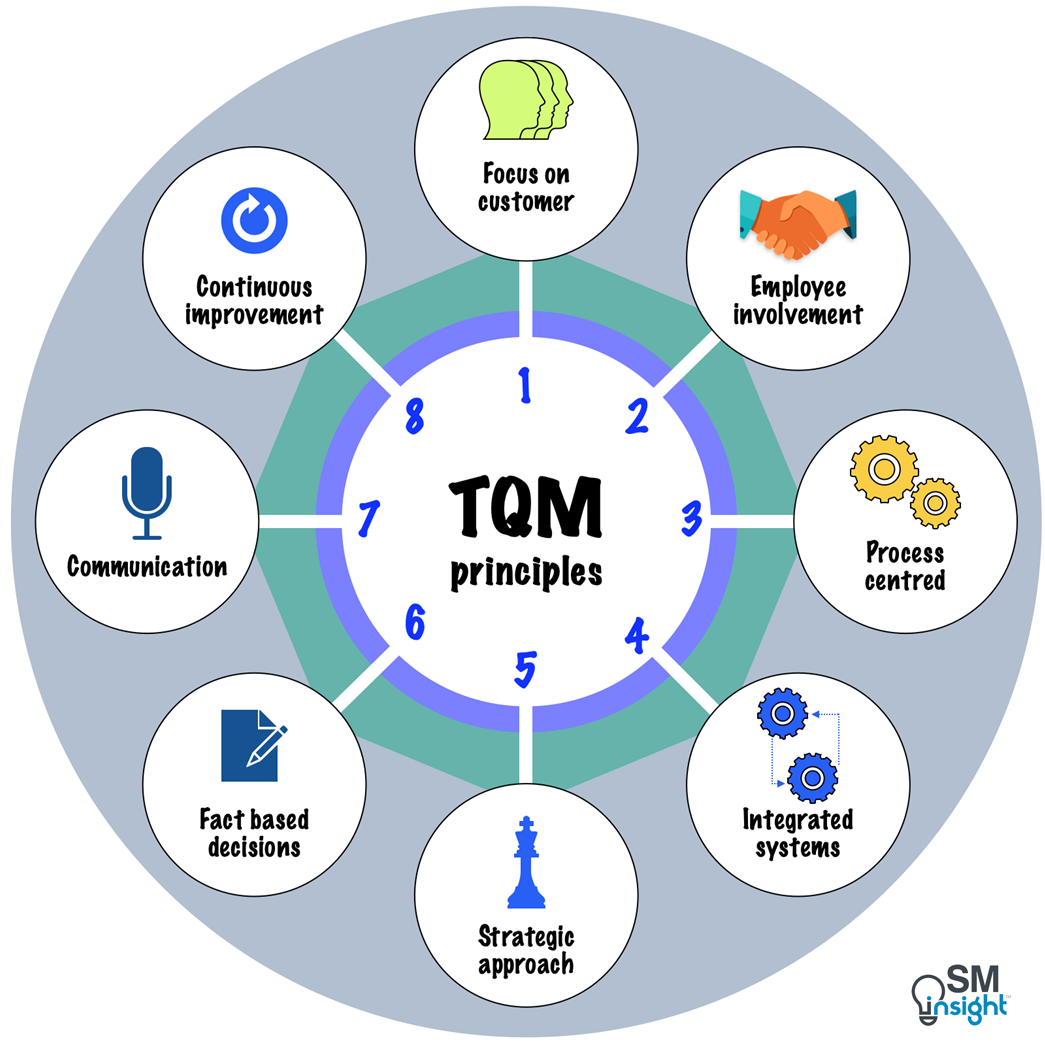
1. Customer Focus
Organizations depend on their customers and, therefore, should understand the current and future needs of the customer, meet customer requirements, and strive to exceed customer expectations.
To become a customer-focused organization, the following steps are crucial:
- Understanding customer needs and expectations (product, price, dependability, etc.)
- Balancing the needs and expectations of customers vs. other stakeholders (owners, employees, suppliers, and society at large).
- Communicating the customer’s needs and expectations throughout the organization.
- Measuring customer satisfaction & acting on results.
- Managing customer relationships.
2. Employee involvement
Employees in all roles and at all levels must be involved and aligned with the organization’s objectives and must be committed to continuous improvement.
Total employee commitment can be achieved through the following:
- Ownership and accountability in problem-solving.
- Driving off fear from the workplace.
- Empowering employees (For example: Creating self-managed work teams).
- Creating an environment that motivates continuous improvement.
- Developing high-performance work systems to integrate continuous improvement efforts with normal business operations.
3. Process-centered approach
A fundamental part of TQM is a focus on process thinking. A process is a series of steps that take inputs from suppliers (internal or external) and transform them into outputs that are delivered to customers (either internal or external).
The below figure shows a generic process model:
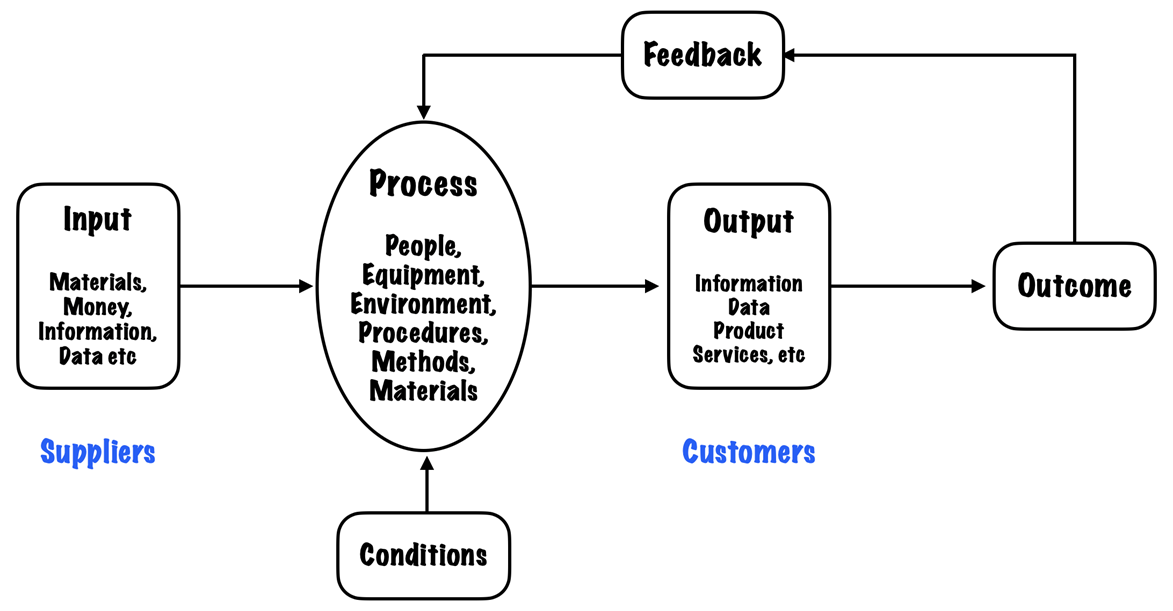
TQM’s process-centered approach requires that all activities in the organization, either business or production process, should be viewed as a process. All such processes should be made effective, efficient, and adaptable by:
- Regularly anticipating changes in customer needs
- Eliminating waste and rework
- Maintaining constructive dissatisfaction with the present level of performance (to enable continual improvement)
- Having progressive performance measures (e.g., reducing cycle time, use of control charts, etc.)
- Using benchmarking to improve competitive advantage.
- Bringing in innovative breakthroughs.
- Using technical tools such as Experimental Design, Quality Function Deployment and so forth.
4. Integrated systems
Since most firms contain a number of departments, each with its own set of functions and goals, they often operate in silos. This brings sub-optimum results to an organization.
TQM focuses on the horizontal processes interconnecting these functions and compels an organization to take an integrated systems approach through well-defined policies, standards, objectives, and processes.
This approach connects business improvement elements with each other to continually improve and exceed the expectations of customers, employees, and other stakeholders.
Some of the key points addressed through this approach are:
- Defining systems by identifying and developing sub-processes under a given objective.
- Using flowcharts and visual aids to assist employees in understanding how their roles fit into the overall organization.
- Structuring the system to achieve customer objectives in the most efficient way.
- Understanding interdependencies among processes.
5. Strategic and systemic approach
TQM takes a strategic approach to planning and management by formulating a strategic plan with quality as its core component. It involves identifying, analyzing, and managing interrelated processes as a system to achieve organizational goals more effectively and efficiently.
By taking a system-of-processes approach, TQM brings together individual processes within a development or manufacturing cycle to be controlled as one.
6. Fact-based decision-making
Effective decisions are always based on the analysis of data and information. TQM requires that an organization continuously collects and analyses data to increase decision accuracy, build consensus, and make predictions based on the past.
7. Communication
Effective communication plays a crucial role in maintaining morale, motivating employees, and reducing process errors. TQM requires that all members within an organization be aware of the plans, strategies, and procedures that will be employed to meet objectives.
This can be achieved by:
- Establish a formal communication channel such that employees are aware of updates, policy changes, and new processes.
- Involving everyone in decision-making to the extent possible.
- Ensuring that employees are aware of their responsibilities and how they relate to the rest of the organization and its overall objectives.
8. Continuous improvement
Organizations that adopt TQM principles have continual improvement as a permanent objective. It drives the organization to be both analytical and creative in finding ways to become more competitive and more effective in meeting stakeholders’ expectations.
Since customer expectations keep shifting, an organization that constantly looks for improvements in operations and its products and services naturally delights its customers.
Total Quality Management requires a cultural shift
The purpose of TQM is to provide a quality product and/or service to customers, which will, in turn, increase productivity and lower costs. This requires a cultural shift that is substantial and difficult to accomplish in a short period of time. It must be approached gradually and methodically.
The table below compares the TQM approach for typical quality elements:
Quality Element | Previous State | TQM Approach |
---|---|---|
Definition | Product Oriented – Customers must take what the company offers in terms of quality | Customer Oriented – Everything is aligned to complete customer satisfaction |
Priorities | Second to service and cost | First among equals of service and cost |
Decisions | Short-term | Long-term |
Emphasis | Detection | Prevention |
Errors | Operations (People make mistakes) | System (Processes provoke errors) |
Responsibility | Quality Control (Individuals are responsible for errors) | Everyone (All employees are responsible for errors) |
Problem Solving | Managers | Teams |
Procurement | Price (Purchase from many suppliers) | Life-cycle costs, Partnerships (Partner with a few suppliers) |
Manager’s Role | Plan, Assign, Control and Enforce | Delegate, Coach, Facilitate and Mentor |
Goal | Zero defects are not achievable | Zero defect is the goal |
The Total Quality Management Framework
TQM has evolved over a period through practice and the contribution of principles by various gurus in the field of quality. The TQM way of product realization is by continuously identifying activities and processes for incremental and breakthrough improvement so as to provide the best to the customer.
TQM achieves this by a combination of various principles, practices tools and techniques, as shown:
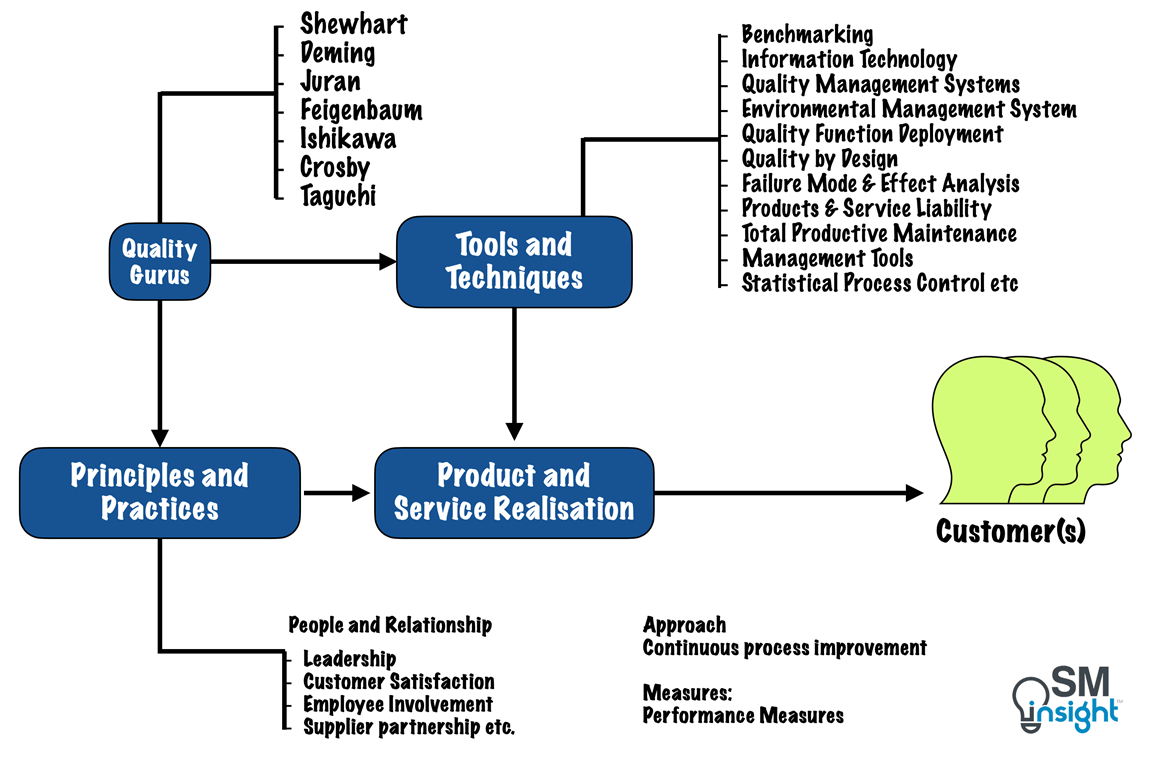
Approaches to implementing Total Quality Management
Each organization is unique in terms of culture, management practices, its products or services, and the processes used to create and deliver them. Hence, no one solution is effective for planning and implementing TQM in all situations.
While the TQM strategy varies from organization to organization, the eight key elements discussed earlier should be present.
Below is a twelve-step generic model that organizations can use as a starting point to implement TQM[18]:
- Top management commitment: Top management learns about TQM and decides to commit to it. TQM is identified as one of the organization’s strategies.
- Assess current state: The organization assesses current culture, customer satisfaction, and QMSs.
- Identify values and principles: Top management identifies core values and principles to be used and communicates them across the organization.
- Develop a master plan: A TQM master plan is developed on the basis of steps 1, 2, and 3.
- Identify and prioritize: The organization identifies and prioritizes customer demands and aligns products and services to meet those demands.
- Map processes: Management maps the critical processes through which the organization meets its customers’ needs.
- Form teams: Management oversees the formation of teams for process improvement efforts.
- Appoint steering committee: The momentum of the TQM effort is managed by the steering committee.
- Contribute: Managers contribute individually to the effort through training, coaching, or other methods.
- Standardize: Daily process management and standardization take place.
- Calibrate: Progress is evaluated, and the plan is revised as needed.
- Recognize and reward: Constant employee awareness through feedback on status is provided, and a recognition/reward process is established.
To develop TQM, organizations can use the above model along with the strategies listed below.
A successful strategy is usually the one that works best for the organization. It is a combination of various philosophies, theories, adaptations of successful techniques, and tools used by others, all combined to address the uniqueness of the organization.
Strategy 1: The TQM element approach
This approach is based on the use of TQM tools to foster improvements and was widely used in the early 1980s as companies tried to implement parts of TQM as they learned them.
Examples of this approach include:
- Quality Circles – a participatory management technique that enlists the help of employees in solving problems related to their own jobs.[18]
- Statistical Process Control – the use of statistical techniques to control a process or production method.[19]
- Taguchi methods – statistical methods that were originally developed to improve the quality of manufactured goods but have more recently been used even in engineering, biotechnology, marketing and advertising.[20]
- Quality Function Deployment – a structured method that uses the seven management and planning tools to identify and prioritize customers’ expectations quickly and effectively. It helps transform the voice of the customer into engineering characteristics for a product.[21]
While some gain is achieved using the element approach to TQM, its overall effectiveness is limited.
Strategy 2: The Guru-approach
This approach uses the teachings and writings of one of the leading quality thinkers as a guide to determine where the organization has deficiencies and then make appropriate changes.
For example, Deming’s fourteen points[22] is a good place to start. Organizations can then work on implementing the approach learned.
One limitation of this approach is that it often ignores the values offered by gurus not selected and tends to lead to an elitist perspective (e.g.: “We only follow Deming’s teachings.”)
Strategy 3: The organization model approach
In this approach, individuals or teams visit organizations that have successfully adopted TQM and determine their processes and reasons for success. They then integrate the ideas and learnings with their own ideas to develop a model specific to their organization.
This method was also used widely in the late 1980s and is exemplified by the initial winners of the MBNQA. However, one limitation of the method is the tendency to copy what is learned, thus limiting originality.
Strategy 4: The Japanese total quality approach
Organizations using this approach examine the detailed implementation techniques and strategies employed by Deming-Prize-winning companies and use this experience to develop a long-range master plan for in-house use.
Florida Power and Light used this approach which won it the Deming Prize.[23]
One limitation of this approach is that it needs to be integrated into the organization’s culture and continually sustained, or it fades away.
Strategy 5: The award criteria approach
Similar to the previous approach, organizations using this approach select the criteria of a quality award, for example, the European Quality Award[24], or the Baldrige Performance Excellence Program[25] to identify areas for improvement.
Under this approach, TQM implementation focuses on meeting specific award criteria. While critics argue that this is not an appropriate use of award criteria, organizations have taken this approach, resulting in notable improvements.
Benefits of Total Quality Management
Numerous studies have found strong and positive correlations between quality and productivity. Efforts to improve quality, if effective and efficient, can have a significant
impact on a firm’s productivity.
But productivity improvement requires balanced attention to the technical, behavioral as well as management systems. Hence, there is a convergence between organizational productivity improvement and organizational process quality improvement.
TQM helps achieve this through its three-pronged approach, as shown:
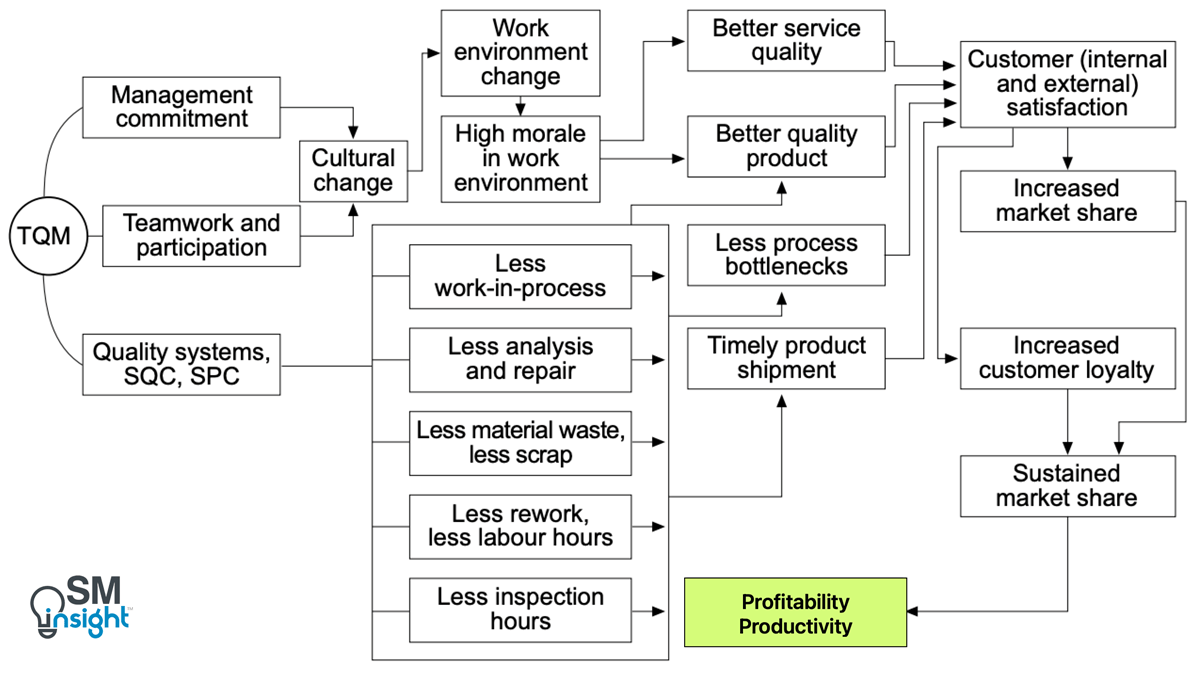
(Source: TQM – Concepts, Evolution and Acceptability in Developing Economies[26])
Organizations implementing TQM have thus experienced numerous benefits, including a strengthened competitive position, adaptability to market changes and regulations, an improved market image, defect and waste elimination, cost reduction, enhanced customer focus and satisfaction, elevated customer loyalty and retention, greater job security, boosted employee morale and enhanced shareholder and stakeholder value.
Difficulties in Total Quality Management implementation
To be successful in their TQM implementation, organizations must create prerequisite conditions (listed below). A sub-optimal approach to fulfilling any of these conditions turns them into obstacles[27]:
1. Management commitment
Organizations that have implemented TQM recommend “management by walking around”, absolutely no delegation of commitment and that the top executive acts as the ultimate teacher.
As companies tailor TQM principles to fit their own organizations, they modify both terminology and structure, thus suggesting that there is no “cookbook approach” to this implementation.
Achieving and demonstrating a personal commitment to TQM principles can be difficult. Top executives have confessed to foundering in some way during the development in expressing top management commitment, providing adequate awareness, skills, and training as well as guidance and clear expectations to middle management prior to “starting.”
2. Structured Approach
A structured approach to continuous improvement is another vital element of TQM implementation. It advocates improving the process, not simply fixing the problems.
The transition from conventional decision-making based on “gut feel” or without “competing strategies” to one using data in steps of process definition, measurement, improvement, and control is an important change that is not easy to adopt.
Only when this change is institutionalized does a continuous improvement process endure even after the top executive moves on to other responsibilities. Such a step requires the use of formal policies, systems, and structures as well as flexible, re-assessable implementation plans.
3. Education and Training
Education and training are mandatory to overcome the lack of understanding of TQM principles by supervisors, customers, and superiors in the traditional chain of command. And there are no shortcuts to it.
Participants can feel discouraged as some of the TQM tools, such as statistical process control techniques, require math skills. In the area of human relations, a majority of the workforce may not have experience in group dynamics.
Facilitating follow-up applications is also more important than the number of people trained as “decay from the classroom to the workplace” can easily take place without immediate practice and coaching.
TQM is a philosophy, and one can teach a lot about it, but without balancing with the knowledge of the right tools and techniques, a workforce cannot be transformed. Top management must insist on the transfer of principles to jobs.
4. Performance Evaluation
Often, organizations implementing TQM find their existing appraisal systems to be contrary to TQM principles.
Traditional appraisal systems are designed to encourage competition which can lead to suboptimization of the organization’s goals. They can reduce objectivity as an employee’s performance is often linked to systems and processes outside his or her control.
Organizations can start by rewriting job descriptions to align with organization-wide objectives, as opposed to divisional or departmental objectives. However, as appraisals concern promotions and career development, transition can be hard.
5. Resistance to change
Resistance to change is an obstacle to TQM implementation that is most frequently cited by organizations implementing it. Resistance can be due to several reasons, such as:
- People think TQM is a program and not a philosophy
- They have “too much to do” because they see quality as an addition and not part of the job
- Sections of management may have a vested interest in the old system
Organizations can address such resistance by reducing fear through communication, education, and sharing power and information to empower the workforce.
6. Relentless pursuit of quality transformation
TQM calls for a change in an organization’s culture which is a gradual and difficult process. Since TQM results take time, the tendency to focus on short-term profits rather than on long-term goals is strong. Maintaining focus on the gradual transition from the “results-oriented” to the “process-oriented” method can be challenging, especially when benefits are accrued far ahead in time.
Sources
1. “International Organization for Standardization”. International Organization for Standardization, https://www.iso.org/home.html. Accessed 05 Oct 2023
2. “Total Quality Management: For Anna University”. Dale H. Besterfield, Carol Besterfield-Michna, Mary Besterfield-Sacre, Glen H. Besterfield and Hemant Urdhwareshe, https://www.google.co.in/books/edition/Total_Quality_Management_For_Anna_Univer/OYb1911sBDMC?hl=en. Accessed 05 Oct 2023
3. “Total quality management”. The Economist, https://www.economist.com/news/2009/11/16/total-quality-management. Accessed 04 Oct 2023
4. “Quality on the Line”. Harvard Business Review (David A. Garvin), https://hbr.org/1983/09/quality-on-the-line. Accessed 04 Oct 2023
5. “HISTORY OF TOTAL QUALITY MANAGEMENT”. American Society for Quality, https://asq.org/quality-resources/total-quality-management/tqm-history. Accessed 04 Oct 2023
6. “Total Quality Management (TQM)”. Inc.com, https://www.inc.com/encyclopedia/total-quality-management-tqm.html. Accessed 04 Oct 2023
7. “Malcolm Baldrige National Quality Award”. Wikipedia, https://en.wikipedia.org/wiki/Malcolm_Baldrige_National_Quality_Award. Accessed 08 Oct 2023
8. “Total Quality Management”. Wikipedia, https://en.wikipedia.org/wiki/Total_quality_management. Accessed 09 Oct 2023
9. “Total Quality Management – more than just Quality Management”. GBTEC Software AG, https://www.gbtec.com/resources/total-quality-management/. Accessed 06 Oct 2023
10. “Walter Andrew Shewhart”. MacTutor, https://mathshistory.st-andrews.ac.uk/Biographies/Shewhart/. Accessed 05 Oct 2023
11. “ABOUT DR. W. EDWARDS DEMING”. Deming.org, https://deming.org/learn/about-dr-deming/. Accessed 05 Oct 2023
12. “Dr. Joseph M. Juran”. Juran.com, https://www.juran.com/about-us/dr-jurans-history/. Accessed 05 Oct 2023
13. “Armand V. Feigenbaum”. Wikipedia, https://en.wikipedia.org/wiki/Armand_V._Feigenbaum. Accessed 08 Oct 2023
14. “Kaoru Ishikawa”. Wikipedia, https://en.wikipedia.org/wiki/Kaoru_Ishikawa. Accessed 05 Oct 2023
15. “Philip B. Crosby”. Wikipedia, https://en.wikipedia.org/wiki/Philip_B._Crosby. Accessed 05 Oct 2023
16. “Genichi Taguchi”. Wikipedia, https://en.wikipedia.org/wiki/Genichi_Taguchi. Accessed 08 Oct 2023
17. “THE ASQ CERTIFIED MANAGER OF QUALITY/ORGANIZATIONAL EXCELLENCE HANDBOOK, FIFTH EDITION”. American Society for Quality, https://asq.org/quality-press/display-item?item=H1569. Accessed 08 Oct 2023
18. “Quality Circles”. Inc.com, https://www.inc.com/encyclopedia/quality-circles.html. Accessed 08 Oct 2023
19. “WHAT IS STATISTICAL PROCESS CONTROL?”. American Society for Quality, https://asq.org/quality-resources/statistical-process-control. Accessed 08 Oct 2023
20. “Taguchi methods”. Wikipedia, https://en.wikipedia.org/wiki/Taguchi_methods. Accessed 08 Oct 2023
21. “Quality function deployment”. Wikipedia, https://en.wikipedia.org/wiki/Quality_function_deployment. Accessed 08 Oct 2023
22. “Fourteen points”. The W. Edwards Deming Institute, https://deming.org/explore/fourteen-points/. Accessed 08 Oct 2023
23. “For Florida Power and Light After the Deming Prize: The”. Dokumen, https://dokumen.tips/documents/for-florida-power-and-light-after-the-deming-prize-the-florida-power-and-light.html. Accessed 09 Oct 2023
24. “European Quality Award”. Oxford Reference, https://www.oxfordreference.com/display/10.1093/oi/authority.20110803095801555. Accessed 08 Oct 2023
25. “BALDRIGE PERFORMANCE EXCELLENCE PROGRAM”. National Institute of Standards and Technology, https://www.nist.gov/baldrige. Accessed 08 Oct 2023
26. “Total Quality Management : Concepts, Evolution and Acceptability in Developing Economies”. R. P. Mohanty and R. R. Lakhe , https://www.researchgate.net/publication/245506809_Total_Quality_Management_Concepts_Evolution_and_Acceptability_in_Developing_Economies. Accessed 08 Oct 2023
27. “Total Quality Management in Ten Exemplary Department of Defense Organizations: Lessons Learned, Innovative Practices, and Quality Measurements”. Naval Postgraduate School, United States Navy, https://www.researchgate.net/publication/235161822_Total_Quality_Management_in_Ten_Exemplary_Department_of_Defense_Organizations_Lessons_Learned_Innovative_Practices_and_Quality_Measurements. Accessed 09 Oct 2023