What is the Theory of Constraints
Theory of Constraints (TOC), a process improvement approach that aims to improve the performance and profitability of any system by identifying and eliminating the “constraint” that limits its output, throughput, and goal achievement.
Dr Eliyahu Goldratt[1], an Israeli physicist turned management guru, conceived the Theory of Constraints and introduced it through his bestselling 1984 novel, “The Goal”.[2] Since then, TOC has continued to evolve and develop and is today a well-known management best practice.
Why use Theory of Constraints
An independent study on the application of the Theory of Constraints (TOC) in various companies yielded the below findings:[3]
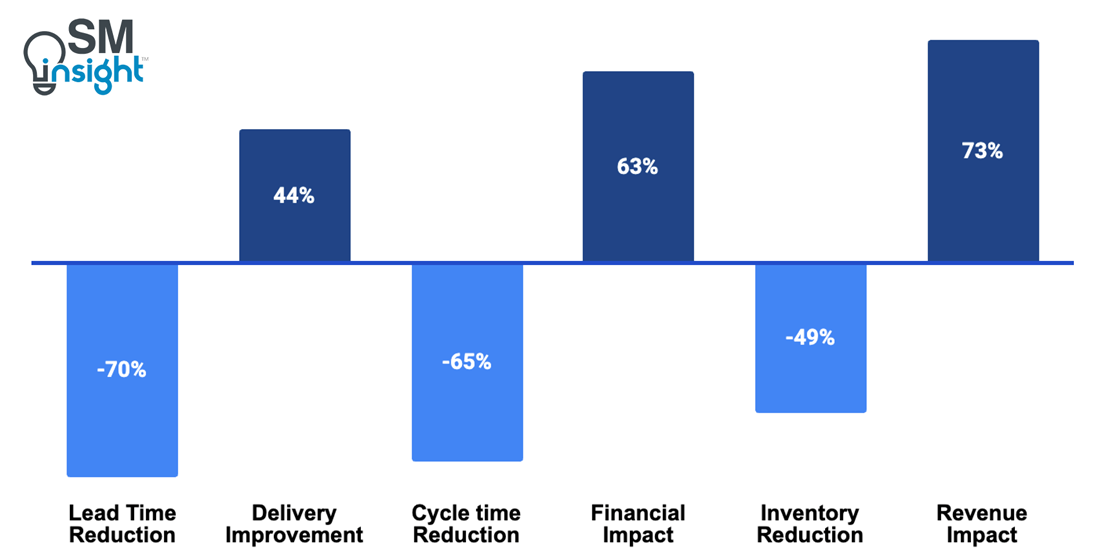
Over the years, the principles of TOC have proven instrumental in enabling organizations to achieve profitability through enhanced performance, strategic market positioning, robust financials, proactive problem-solving (rather than firefighting), improved customer service, prevention of conflicts and more.
TOC principles have been used in a wide range of industries and domains from manufacturing to software development to project management to healthcare.
The Goal in Theory of Constraints
To identify constraints in any system, it is important to define what an organization intends to achieve. This raises the question – what is the goal of an organization?
According to TOC, the one and only goal of any for-profit organization is to make money.
In a plethora of conflicting objectives and operational targets, the relationship between actions taken on the ground versus the money it generates for the organization is often lost or is vague at best. Hundreds of key performance indicators (KPIs) make it difficult for organizations to focus on what is important.
TOC addresses this problem by defining the Goal in terms of just three key measurements – Throughput, Inventory and Operational expense.
Throughput | The rate at which the system generates money through sales. |
Inventory | The money that the system has invested in purchasing things that it intends to sell. |
Operational expense | The money the system spends in order to turn inventory into throughput. |
The goal of an organization is to increase throughput while simultaneously reducing both inventory and operating expenses.
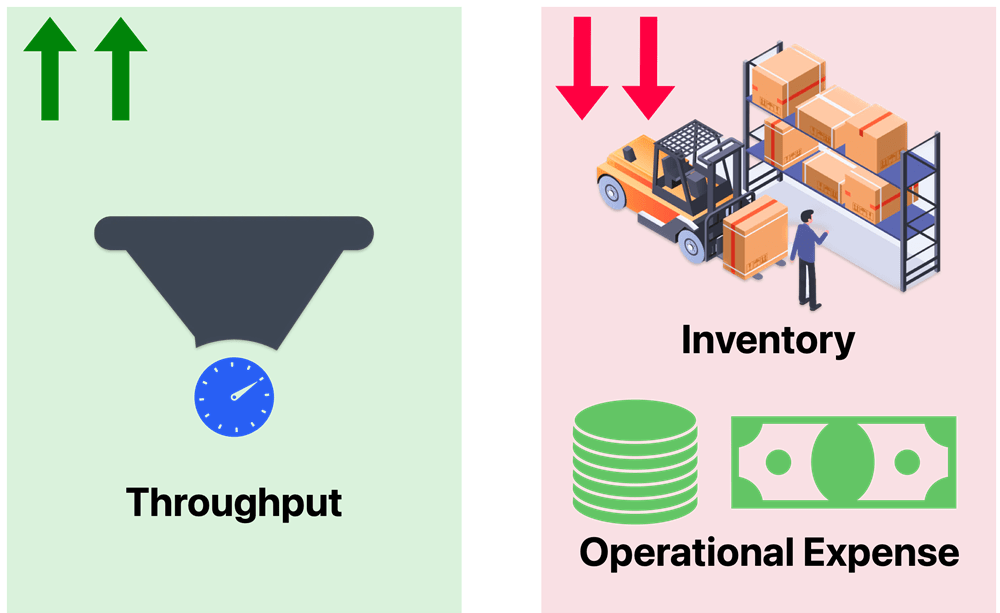
By evaluating an organization’s objective through the Theory of Constraints (TOC) framework, clarity arises as to whether it contributes to the organization’s overarching goal of generating profits.
Everything within an organization fits within the three parameters – Throughput, Inventory and Operational Expense.
For example, a decision to install a machine will lead to higher depreciation costs, which is an operational expense. The current value of that machine is inventory. If the machine improves throughput over and above the burden on inventory and expense, it contributes to the organization’s overall goal.
Similarly, if an organization’s (or a department’s) objective is to improve productivity, any action that moves it towards making money is productive and an action that takes it away from making money is non-productive.
Constraint in Theory of Constraints
A constraint is what “limits a system from achieving higher performance versus its goal”.
For any organization, throughput measures the flow of goods and services to market and a constraint is that which limits the maximum possible flow. In other words, the constraint is what, if the organization had just a little more, would generate higher Throughput.
When driving continuous improvement, organizations are tempted to try to improve everything at once, but it rarely leads to sustained improvement in the overall performance of the organization.
This is because not all improvements are created equal. Only a few improvements/changes impact the constraint and improve throughput while most do not. This seemingly minor distinction makes all the difference.
Example of a Constraint
To demonstrate this concept, consider an automobile manufacturing company whose manufacturing process consists of 5 stage, as depicted in the figure below:
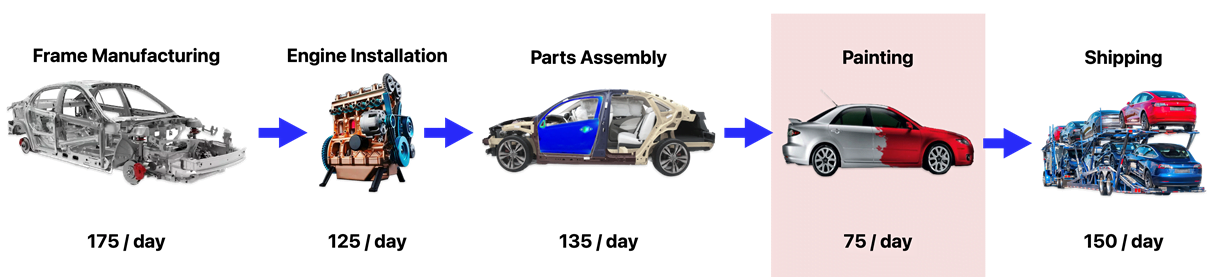
The five stages are – frame manufacturing, engine installation, parts assembly, painting, and shipping. Maximum capacities per day are indicated under each activity.
It can be seen from the figure that the paint shop has the lowest capacity of 75 cars per day. Going by the definition of constraint, this is the current limiting factor for the maximum number of cars that the company can produce.
Suppose the engine installation department decides to invest $15,000 in a new robotic arm that improves the capacity by an additional 25 cars per day. As seen from the figure above, the engine installation capacity would increase from the current 125 per day to 150 per day.
Would this change the throughput?
Unfortunately, this would have no impact on the painting process and hence, the throughput would remain unchanged. Such a move would not benefit the company.
Suppose that the company decides to install an additional Painting bay to double the capacity from 75 per day to 150 per day. With this, the constraint will shift to engine installation. With this, the company can manufacture 125 cars instead of 75 cars.
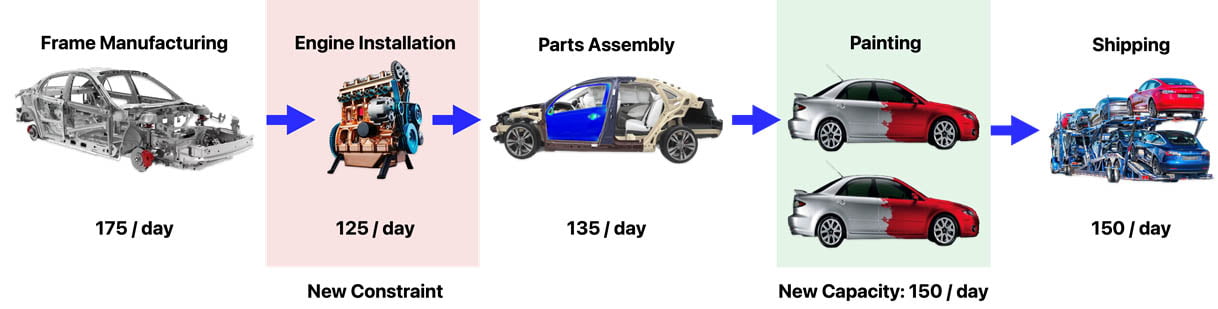
Investing in that robotic arm will now improve throughput. But there is a catch. Notice how the next constraint in the system becomes the parts assembly that limits the production to 135 per day.
The benefit of increased engine capacity will be realized to the extent of an additional 10 cars per day before the constraint shifts to the Parts Assembly which then limits the throughput to 135 cars per day.
In most systems, there is one constraint at a time that limits it from advancing towards its Goal. The central message of TOC is to identify and address such constraints one at a time to improve throughput.
And any improvement in throughput takes the company that much closer to its Goal.
Constraint vs. Bottleneck
A bottleneck is a resource whose capacity is less than or equal to the demand while a constraint is a limiting factor to an organization’s performance. It is the current obstacle to the organization achieving its goal.
A constraint can be called a bottleneck, but a bottleneck is not always a constraint.
Consider the example of the automobile manufacturing company above. Having upgraded the paint and assuming a market demand of 140 cars per day, the constraints and bottlenecks for the company will be as below:[4]
Process | Capacity | Constraint | Bottleneck |
---|---|---|---|
Frame Manufacturing | 175 | No | No |
Engine Installation | 125 | Yes | Yes |
Parts Assembly | 135 | No | Yes |
Painting | 150 | No | No |
Dispatch | 150 | No | No |
Notice how the parts assembly process is not currently a constraint but still a bottleneck. If the engine bay can produce more than 135 cars, the constraint will shift to the next bottleneck, i.e. Parts assembly.
Alternatively, if the market demand itself would be 130 cars per day (instead of 140), then the Engine bay would be the only constraint as well as the bottleneck.
Can there be Multiple Constraints?
In real-world scenarios, processes are far more complicated and involve thousands of sequential as well as non-sequential sub-processes that come together to form the final product (or service).
Such systems could sometimes have more than one constraint but in most cases, current constraints are only a handful.
It is important to note that Every independent path of flow will have its own constraint, but the system (as a whole) will still have one (or two) constraint(s) as the limiting factor to the overall flow.
TOC encourages focusing on one or two constraints at a time and exploiting them to improve throughput.
Types of Constraints
Constraints can be both internal and external to the organization.
They can also be classified as Equipment-based (where the way equipment is used limits the system’s ability), People-based (lack of skills or wrong knowledge and beliefs), and Policy-based (written or unwritten policies that prevent the system from making more).
Examples of some of the constraints are as below:
Capacity Constraint (internal): This is when the current ability to deliver is less than the market demand for those products or services.
Like in the example above, a company in this situation typically has a backlog of sales orders, low delivery performance, and/or stockouts. By the principle of TOC, the real test of an internal capacity constraint is very high utilization of at least one internal resource (95%+).
Cash Constraint (internal): This is when a company’s ability to source inputs is less than market demand due to the inability to pay suppliers. This situation can also be triggered when suppliers blacklist an organization due to late payments and/or disputes may have been taken to court.
Suppliers typically expect upfront payments in such cases and a small increase in cash usually can increase sales, throughput, on-time delivery and available cash in a relatively short amount of time.
Regulations and Standards (internal/external): Regulations and standards can limit a system’s time and level of use. These can be quotas, schedules, or mandatory. For example, reducing the speed of a machine between 22:00 hrs. to 06:00 hrs. to control noise levels.
Demand Constraint (external): This is where the market demand at current prices is less than the rate at which a company could produce the product or service.
When a company begins eliminating its internal constraints, they shift and eventually, the supply outnumbers the orders that the company could secure. In such a situation, all backlog orders are fulfilled, and production is limited by the number of orders.
Though this is an external constraint, it can be addressed through focused marketing efforts or providing bulk discounts if the economics works out.
Market Constraint (external): this is where a company captures the bulk of the market and runs out of further space to grow.
For example, Google Search occupies almost 90% of the search engine market share and has limited potential to increase its user base significantly. Unless the market itself expands, there is little chance that it could double its user base in a short span as it did very easily in its growth years.
Supply Constraint (external): This is when a company is unable to meet all its demand due to shortages in input materials/services. For example, chip shortages triggered during the pandemic impacted almost every company in the automobile and electronics sector.[3]
Dependent Events, Statistical Fluctuations & the Origin of Constraints
A balanced plant is an ideal system where the capacity of all resources is trimmed to exactly match the market demand. In such a system, every resource works to its full capacity and is optimally utilized. There are no constraints in such a system, which operates at peak efficiency with zero wastage.
The only problem is that such a plant does not exist.
Two factors make it difficult to achieve such a balance. Dependent Events and Statistical Fluctuations.
In any plant process, an event, or a series of events, must take place before another can begin. The subsequent event depends upon the ones before it. This is called a dependent event.
Likewise, in these processes, some types of information can be determined precisely while others cannot. These types of information vary from one instance to the next and are subject to statistical fluctuations.
For example, it’s possible to predict whether a computer-controlled robot will complete an assembly in precisely 56 seconds, but it is not possible to predict if a truck will arrive at the loading bay precisely at 9:15 AM.
When companies operate complex processes with thousands of variables, most of the factors critical to running them successfully cannot be determined precisely ahead of time. When a fluctuation occurs in one of the sub-processes, a constraint is created.
The Five Focusing Steps of Theory of Constraints
The Theory of Constraints proposes a five-step process to improve efficiency and achieve higher throughput. While originally applied to the manufacturing process, these steps today are used in a wide range of industries, from production to finance to healthcare. They are depicted in the figure below:
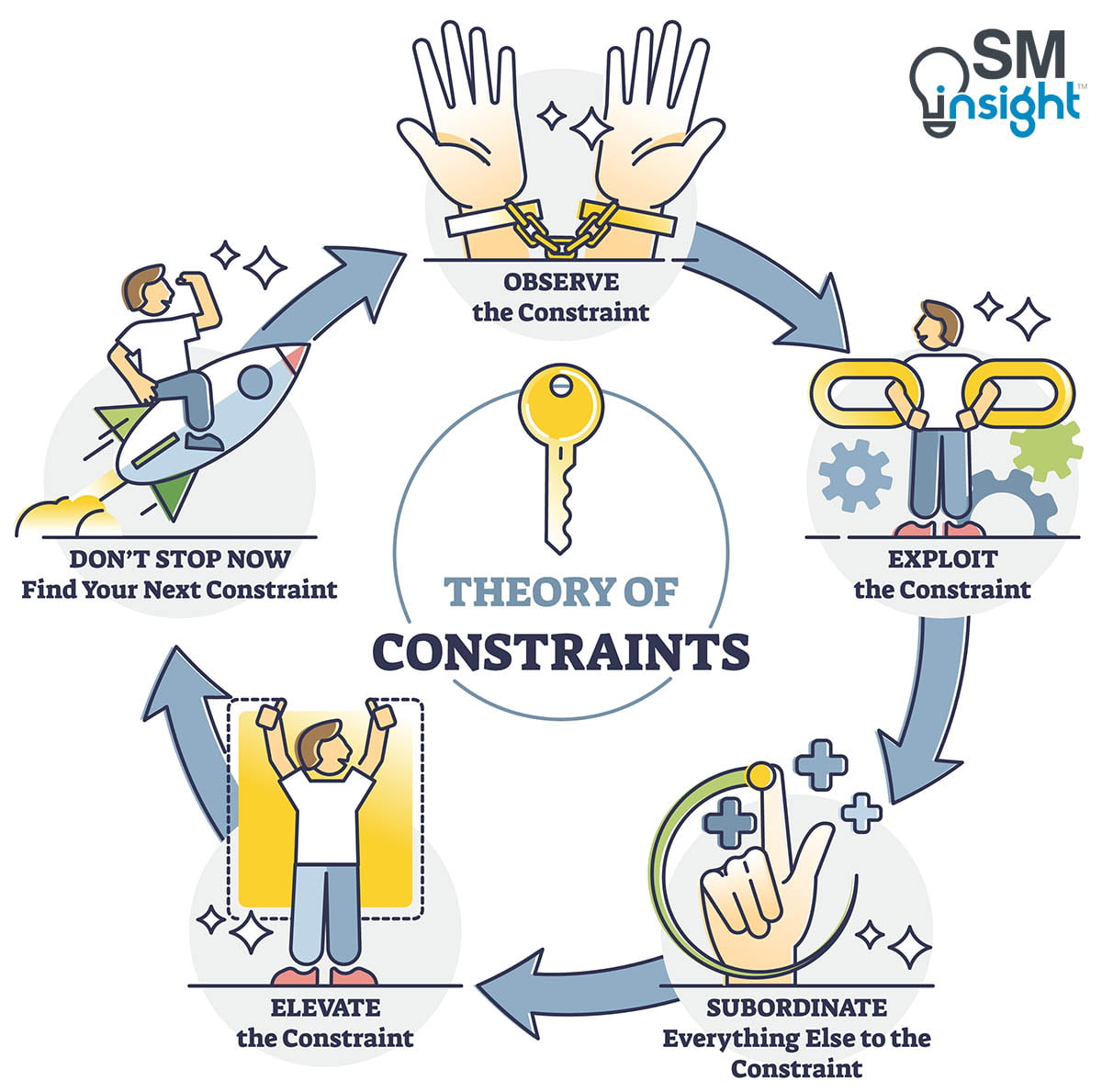
Step 1: Identify the constraint
In any system, a constraint always exists, or else production would be infinite. Identifying a constraint begins with the research of the bottlenecks – the weak links in the system.
Production bottlenecks are generally known and easy to identify. If not, a good way to find would be to spot signs of inventory pileup upstream where parts wait to get processed. Similarly downstream, resources are under-utilized as they wait for parts to arrive through the constraint.
Non-production bottlenecks are a bit tricky to locate. They could range from bad planning to poor skills to an engineering practice that is followed but not actually needed etc. These can be identified using the TOC thinking processes discussed later in this article.
Step 2: Exploit the constraint
To exploit a system’s constraint is to make sure the constraint is fully utilized. This step aims to identify the factors that negatively impact the constraint’s workflow and eliminate/mitigate their impact.
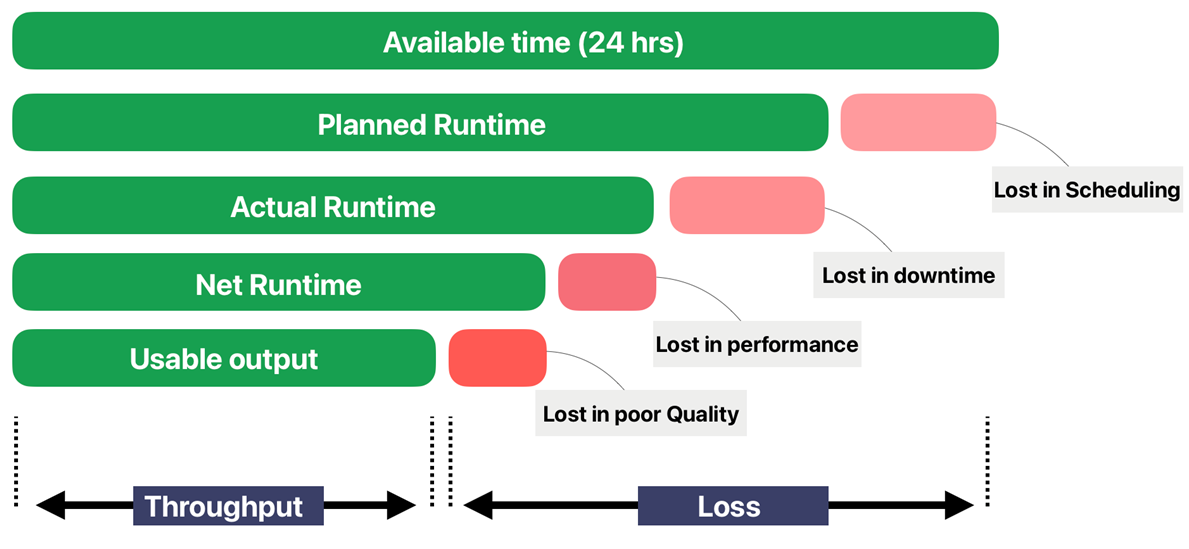
The figure above shows typical losses for a production line resource. If this resource were to be a constraint, then exploiting the resource, in this case, would mean:
- Adjusting the schedule for a 24-hour operation.
- Minimizing downtime through preventive maintenance, maintaining a buffer stock of spare and tools, and scheduling maintenance during changeover/loading.
- Optimizing the machine’s performance to operate close to its maximum capacity, including determining the optimal batch size and appropriate loading techniques.
- Implementing rigorous quality control measures to identify errors in input materials, with a focus on upstream quality control rather than downstream.
In this step, any potential inefficiencies related to uptime and productivity must be eliminated as they directly impact the company’s overall productivity.
On the contrary, if the resource is not a constraint, the principles of the TOC suggest a different approach. In such cases, it is advisable to allow the resource to remain idle or underutilized which brings us to Step 3.
Step 3: Subordinate everything else to the Constraint
A constraint cannot be exploited (Step 2) in insolation as processes operate in “chains”. Any changes made to a constraint located mid-process will have an impact on the previous as well as the subsequent processes.
Such impact could be in the form of slowing down/speeding up downstream processes, producing more at some stations while less at another, or making changes to the number of intermediate parts which are buffer inventory.
Often, this can mean higher costs/time in operating some of the non-constraint processes. To subordinate a constraint implies making such modifications despite them appearing suboptimal at a local level.
The idea is to avoid local optimization and focus on constraint optimization.
TOC provides an effective tool to manage this process called the Drum-Buffer-Rope (DBR).
DBR originated in Goldratt’s first book “The Goal”[2], but got its name later in his book “The Race”.[5]
DBR is a constraint-aware workflow control process in which the “drum” beat sets the pace of production based on the constraint’s capacity, the “buffer” provides a contingency, and the “rope” controls the flow of work.
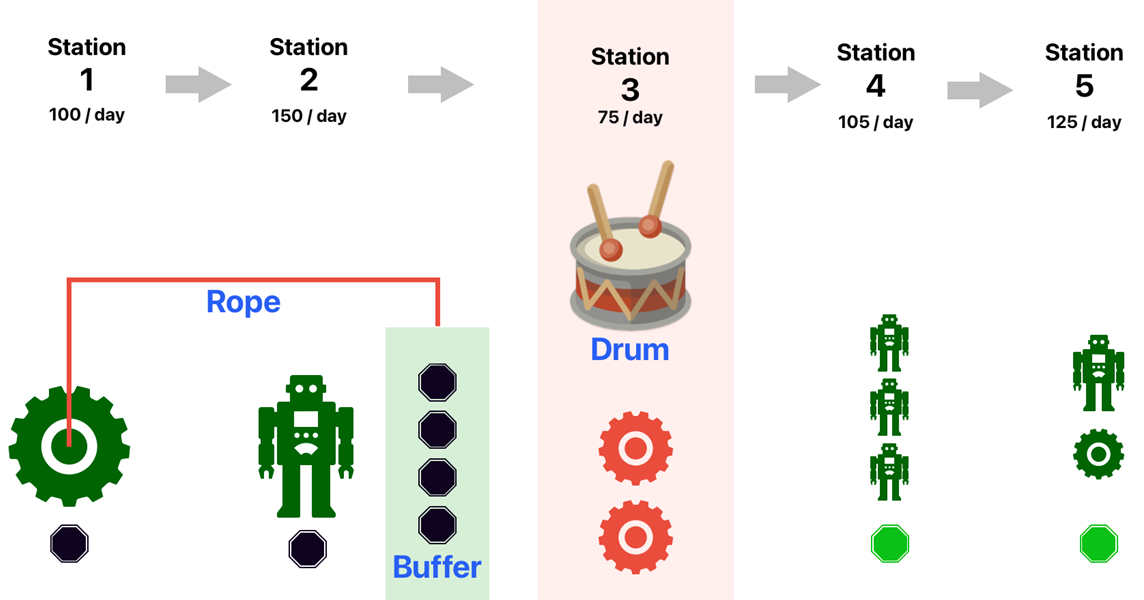
In the manufacturing example (figure above), the drum is the bottleneck, i.e. Station-3 which has the lowest capacity of 75 parts/day. This also governs the system’s throughput.
The buffer is the material upstream of the constraint, which is to make sure the drum is never starved. This is to address any fluctuations in previous stations.
The rope is a signal or information from the buffer to the beginning of the line (Station-1). If the drum processes parts, the parts in the buffer move forward. The rope then sends information to replenish another part at the beginning of the line.
Notice how stations 1 & 2, which have capacities higher than the constraint, will be under-utilized. The central idea of Step-3 (subordinating everything else) is to let this happen as it does not impact the throughput.
If stations 1 & 2 were allowed to run at full capacity, the corresponding accumulation of inventory (before station 3) would increase expenses without improving throughout – a move that would take the process away from its Goal.
Step 4: Elevate the Constraint
In this step, more substantive changes are implemented to break the constraint. These steps might involve a significant investment of time and/or money.
The key action in this step is to weigh the impact of additional investments like bringing in a new resource or major process modifications using the throughput accounting metrics (throughput/inventory/operational expense) and implement them to improve the throughput.
Step 5: Find the next constraint (Back to step 1)
When constraints are elevated (Step-4), they cease to be bottlenecks, allowing attention to shift toward the next limiting factor in the process – the new Constraint.
This necessitates a return to Step-1 until the new constraint is optimized. Eventually, the constraint may shift towards external factors such as market demand. In such cases, the company can address this by concentrating on cost-reduction strategies to enhance competitiveness or by intensifying marketing efforts.
This is the TOC’s ongoing process for continuous improvement.
The Theory of Constraints Thinking Process
TOC applies the cause-and-effect thinking processes used in the hard sciences to understand and improve organizations. The process is analogous to a clinician treating a patient as follows:
Problem Diagnosis -> Designing a Treatment Plan -> Executing the Treatment Plan
In the language of organization problem-solving, the process is described via the use of three questions:
What to Change?
What to Change To?
How to Cause the Change?
TOC also provides six logical steps that are embedded into these questions and aid in effective organizational problem-solving as discussed below:[3]
What to Change?
From a list of observable symptoms, cause-and-effect is used to identify the underlying common cause, the core problem, for all the symptoms.
In organizations, the core problem is inevitably an unresolved conflict that keeps the organization trapped and/or distracted in a constant tug-of-war (management versus market, short-term versus long-term, centralize versus decentralize, process versus results). This conflict is called a Core Conflict.
Due to the destructive impact of Core Conflicts, organizations often devise policies, measures, and behaviors to mitigate their adverse effects. When addressing the Core Conflict, these approaches must be eliminated, altered, or substituted.
The process involves two steps:
Step 1: Identify the Core Conflict causing the symptoms, or UnDesireable Effects (UDEs), of the chosen subject.
Step 2: Build a Current Reality Tree (CRT)[8] that validates the identification of the Core Conflict. This helps understand the existing cause-and-effect relationships of the subject and identifies the conspiring formal and informal policies, measurements and behaviors that support the existence of the UDEs.
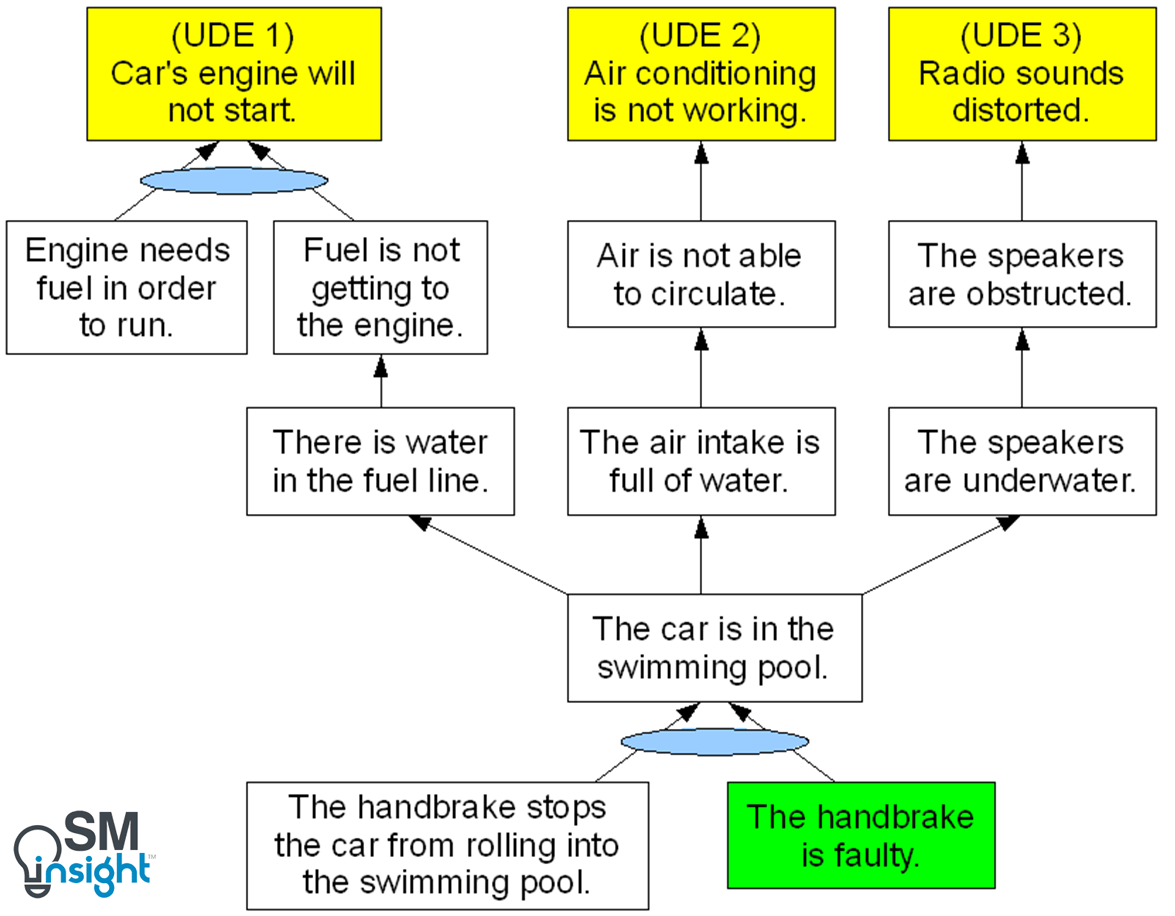
What to Change To?
By challenging the logical assumptions behind the Core Conflict, a solution to the Core Conflict is identified in this step.
Step 3: An Evaporating Cloud (EC)[9] (Also called Core Conflict Cloud) must be constructed to articulate the core conflict clearly. This helps surface hidden assumptions so that some of them can be invalidated.
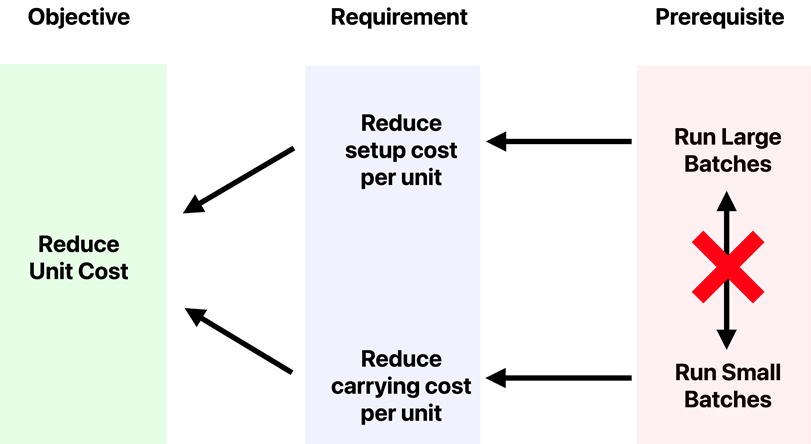
This is only the starting point for the development of a complete solution – a strategy for resolving all the initial symptoms and many others, once and for all.
The strategy must also include the changes that must be made alongside the solution to the Core Conflict to ensure that the solution works and that the organization is restored to its “best possible health.”
These often involve changes to the policies, measurements, and behaviors identified in “What to Change?”, as well as the organization’s strategic objectives.
The strategy is not complete until all potential negative side-effects of the strategy have been identified and the means for preventing or mitigating them become key elements of the strategy.
Step 4: Construct a Future Reality Tree (FRT)[10] that lays out the complete solution/strategy that:
- Resolves all the UDEs
- Ensures alignment with the Strategic Objectives (SO)
- Ensures that no new negative side effects (Negative Branches) will occur
- Identifies what changes in the culture of the system and/or sub-system must be made to ensure the symptoms are resolved
- Leverages the existing TOC applications needed to make the solution/ strategy work
- Quantifies the “bottom line” value of achieving those desired effects and SOs
FRT maps the full implications of the proposed injections (actions that solve the conflict) to ensure that they are sufficient to solve every UDE.
How to Cause the Change?
Considering the unique culture within organizations, a transition plan is developed in this step. This helps move the organization towards strategy realization.
This plan must specify necessary actions, responsible parties, and timelines and must chart the overall course for getting from the Current Reality to the Future Reality.
Step 5: Construct a PreRequisite Tree (PRT)[11]
Details of what each part of the system/sub-system must contribute and when to achieve each of the milestones must be mapped using a PRT.
A PRT takes the complete set of injections (solution elements) from the FRT and sets them as its “objectives.” It then breaks these objectives down into an ordered sequence of intermediate objectives (key milestones) for execution.
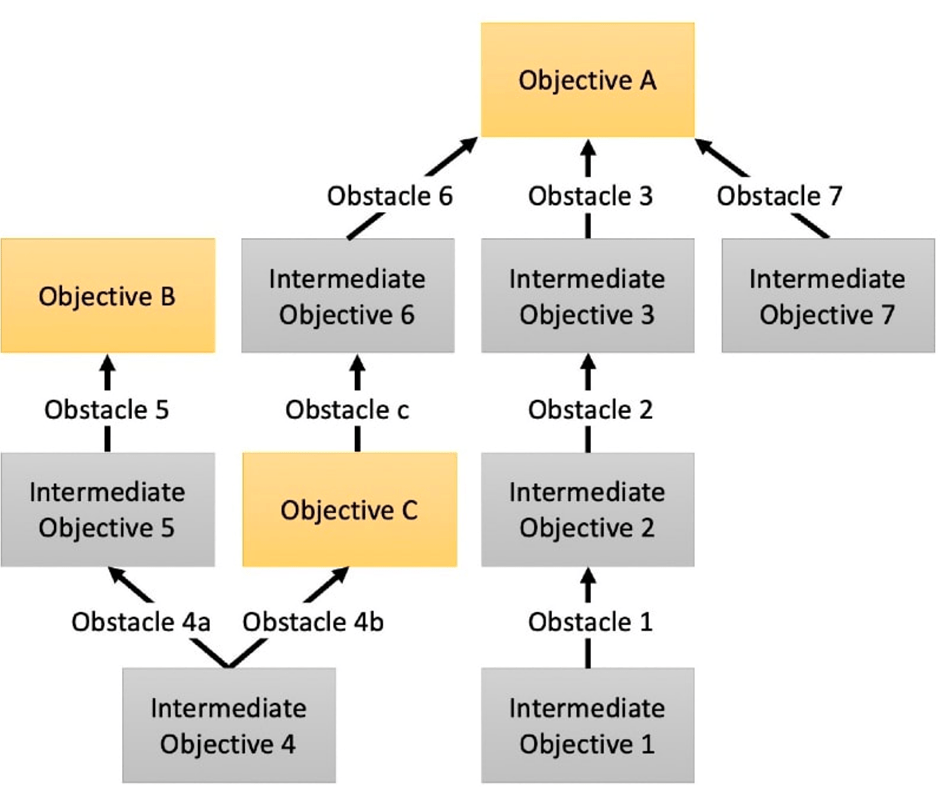
Step 6: The last step is to create a detailed task interdependency diagram using Transition Trees (TRTs). A Transition Tree is a step-by-step sequential depiction of how to implement the change. TRTs combine an entity of current reality, a statement of need and an action (injection) to create a new reality (expected effect).
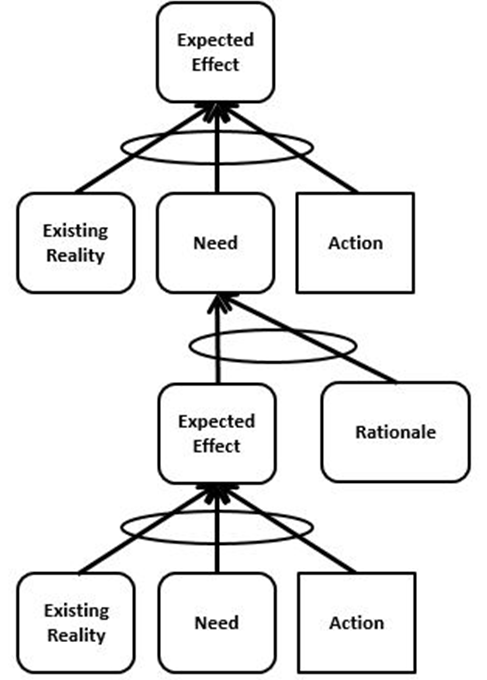
Thus, the three questions—What to Change? What to Change To? and How to Cause the Change?—alongside the Six steps, together form the framework known as the TOC Thinking Process.
Six Layers of Resistance to Change
Building active consensus, collaboration and buy-in is crucial for the success of a plan.
To address this, TOC has developed a process based on the psychology of change that acknowledges and systematically addresses the questions people intuitively ask when evaluating a change.
They are:
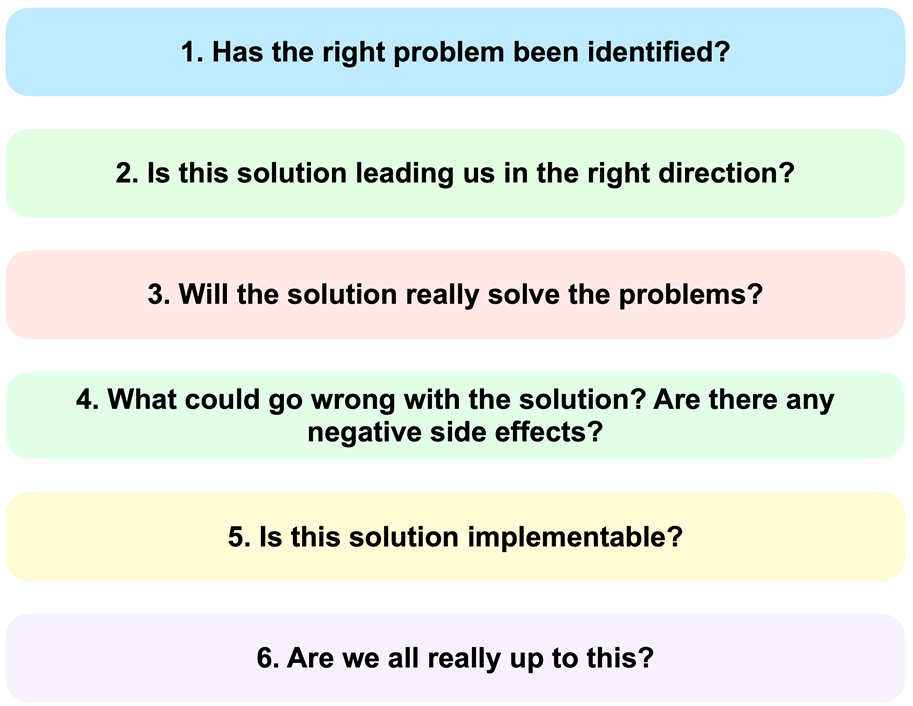
If these questions aren’t answered frankly and effectively (with both the people who must implement and those who will be affected by the change), there will be no buy-in and support. Like most changes, no matter how great the idea or tremendous the value, the strategy and tactics are bound to fail.
The Nine Rules of Theory of Constraint
Before developing the Theory of Constraint, Goldratt, along with other Israeli researchers worked on a theory called Optimized Production Technology (OPT). Developed in the 1970s, OPT is a production management methodology that helps organizations achieve greater profitability and less waste.[7]
TOC has been shaped by the nine rules of OPT that are essential to adapt the TOC mindset. They are:
1. Balance flow, not capacity
By balancing the flow of the products with the market demand, constraints can be eliminated while avoiding excess capacity.
2. An hour lost at a bottleneck is an hour lost for the total system
A bottleneck with no reserve capacity (constraint) governs the system’s throughput. Any loss here is critical and irreversible.
3. An hour saved at a non-bottleneck is just a mirage
The flow remains dependent on the bottleneck. An hour earned on a non-bottleneck does not benefit the system’s throughput but will only increase the inventory.
4. The level of utilization of a non-bottleneck is determined not by its own potential but by some other constraint in the system
By applying the principle of the DBR, non-bottleneck resources must be controlled by the bottleneck. Using non-bottlenecks according to their capacity would only produce excess inventory.
5. Utilization and activation of a resource are not the same
“Utilizing’’ a resource means making use of the resource in a way that moves the system toward the goal. “Activating’’ a resource is like pressing the ON switch of a machine; it runs whether or not there is any benefit to be derived from the work it’s doing.
6. Bottlenecks govern both the throughput and inventory in the system
The overall throughput of the system cannot exceed the amount of the constraint. The blind activation of upstream resources can quickly inflate inventories.
7. The transfer batch may not and often should not be equal to the process batch
The transfer batch, which refers to the number of items moved between process stages, is typically not required to be the same as the process batch size. They can differ due to various factors and considerations to optimize the overall efficiency and effectiveness of the system.
8. The process batch should be variable, not fixed
The process batch, referring to the number of items processed together, should ideally be flexible and adaptable rather than rigidly fixed. This variability allows for better responsiveness to changing conditions, improved efficiency, and optimization of resources based on the specific requirements and constraints of the system.
9. Capacity and priority should be considered simultaneously, not sequentially
By considering them simultaneously, decision-makers can optimize resource allocation based on both the available capacity and the relative importance or urgency of tasks, leading to more effective and efficient utilization of resources within the system.
Throughput Accounting and True Cost of a Constraint
TOC’s Throughput Accounting is an alternative accounting methodology that attempts to eliminate harmful distortions introduced by traditional accounting practices – distortions that promote behaviors contrary to the goal of increasing profit in the long term.
Inventory: traditional accounting treats inventory as an asset, assuming it can be sold for cash. This can lead to producing unnecessary items which inflate assets and generate “paper profit” based on unsellable inventory that also incurs storage costs.
In contrast, the Theory of Constraints views inventory as a liability, as it ties up cash that could be better utilized elsewhere.
Expense: traditional accounting prioritizes expense reduction, while the Theory of Constraints values increasing throughput over cutting expenses. Expense reduction is limited by reaching zero expenses, whereas increasing throughput has no such limitations.
When eliminating constraints, companies encounter situations where expensive or less efficient alternatives could increase throughput. But in such cases, decisions are driven by isolated cost considerations or local optima rather than throughput. This could be counterproductive.
Consider the example in the figure below that illustrates a chain installation bay involving two machines. Assume that the bay is a constraint in the factory. The chain can be installed either by utilizing a cost-effective and efficient machine (Machine-1) only or by also simultaneously utilizing a more expensive and slower machine (Machine-2).
As the process is a constraint, there is a queue of bulldozers (inventory) waiting to complete this process.
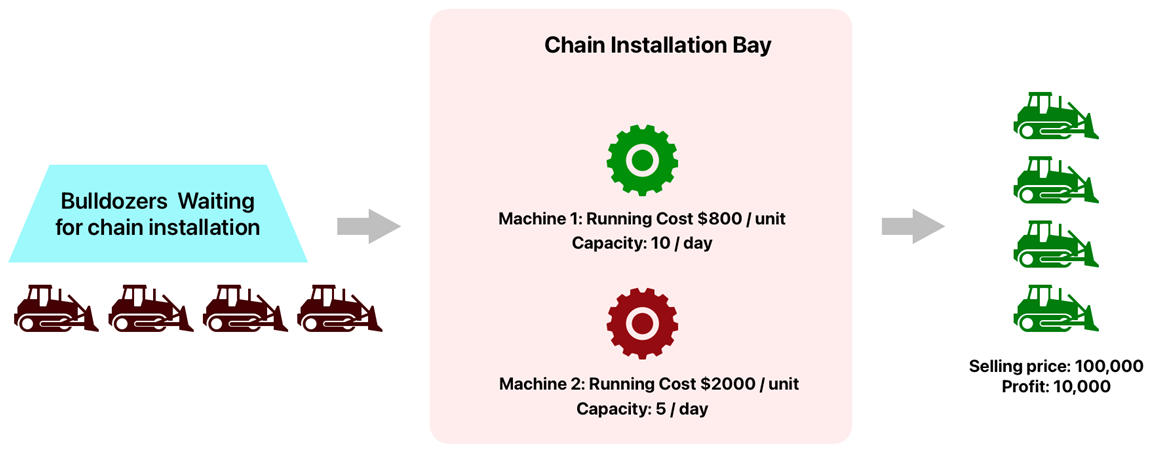
An assembly of a bulldozer where the chain installation process is a constraint
If one looks at the process in isolation, it becomes clear that Machine-2 is both expensive to run and slow, thereby it is ideal to process the load on Machine-1. If the installation bay manager were to make a decision, he/she might choose to reduce costs by using only Machine-1 (cost control is an important KPI for individuals and departments).
It is only when the situation is analyzed using the principles of TOC, the true cost emerges.
Scenario 1: Using only the fast and efficient machine:
Machine-1 | |
---|---|
Processing cost per bulldozer | $ 800 |
Daily Capacity | 10 |
Cost incurred (per day) | $ 8000 |
Revenue generated (per day) | $ 100,000 x 10 = $ 1,000,000 |
Profits (per day) | $ 10,000 x 10 = $ 100,000 |
Scenario 2: Augment capacity using the slower and less efficient machine:
Machine – 1 | Machine – 2 | |
---|---|---|
Processing cost per bulldozer | $ 800 | $ 2000 |
Daily Capacity | 10 | 5 |
Cost incurred (per day) | $ 8000 | $ 10,000 |
Revenue generated (per day) | $ 100,000 x 10 = $ 1,000,000 | $ 100,000 x 5 = $ 500,000 |
Profits (per day) | $ 10,000 x 10 = $ 100,000 | $ 10,000 x 5 = $ 50,000 |
In the second scenario, the company can ship five additional bulldozers per day making an additional revenue of $500,000 and a profit of $50,000 by spending $ 10,000. This takes the company closer to its Goal vs the first scenario of running a single machine.
While unit economics drive decisions in most companies, the goal-optimized process flow in TOC demonstrates how constraint elimination can have a huge impact on the Revenue and Profitability of a company.
Conclusion
In Conclusion, the Theory of Constraints is a powerful management philosophy that helps organizations achieve their goals by focusing on the most critical factor that limits their performance.
It provides a set of tools and methods for identifying and eliminating constraints, analyzing, and resolving problems, measuring, and improving performance, and developing and communicating strategies.
While TOC has helped organizations improve productivity, quality, customer satisfaction, profitability and more, its principles can be equally beneficial when applied to individual problem-solving endeavors.
Sources
1. “Eliyahu M Goldratt”. Wikipedia, https://en.wikipedia.org/wiki/Eliyahu_M._Goldratt. Accessed 21 Jun 2023
2. “The Goal”. Wikipedia, https://en.wikipedia.org/wiki/The_Goal_(novel). Accessed 21 Jun 2023
3. “The Theory of Constraints and its Thinking Processes”. Everydaykanban, https://www.everydaykanban.com/wp-content/uploads/2013/05/the_theory_of_constraints_and_its_thinking_processes.pdf. Accessed 23 Jun 2023
4. “Constraint vs. bottleneck”. CHRIS HOHMANN, https://hohmannchris.wordpress.com/2014/05/06/constraint-vs-bottleneck/. Accessed 22 Jun 2023
5. “Shortage of Legacy Chips Keeping Ford CEO Up at Night”. Bloomberg, https://www.bloomberg.com/news/articles/2022-11-18/shortage-of-legacy-chips-keeping-ford-ceo-up-at-night. Accessed 22 Jun 2023
6. “The Race”. ISBN, https://isbnsearch.org/isbn/9780884270621. Accessed 23 Jun 2023
7. “A Critical Look at Goldratt’s Drum-Buffer-Rope Method”. Christoph Roser (Allaboutlean.com), https://www.allaboutlean.com/drum-buffer-rope/. Accessed 23 Jun 2023
8. “Current reality tree (theory of constraints)”. Wikipedia, https://en.wikipedia.org/wiki/Current_reality_tree_(theory_of_constraints). Accessed 23 Jun 2023
9. “Evaporating Cloud”. Wikipedia, https://en.wikipedia.org/wiki/Evaporating_Cloud. Accessed 24 Jun 2023
10. “What is Future Reality Tree?”. visual-paradigm.com, https://online.visual-paradigm.com/knowledge/problem-solving/what-is-future-reality-tree/. Accessed 23 Jun 2023
11. “Prerequisite Tree (PRT)”. Tocinstitute.org, https://www.tocinstitute.org/prerequisite-tree.html. Accessed 24 Jun 2023
12. “Thinking Processes – Transition Tree”. CHRIS HOHMANN, https://hohmannchris.wordpress.com/2015/07/13/thinking-processes-transition-tree/. Accessed 24 Jun 2023
13. “Learn how OPT acts in process optimization by identifying production bottlenecks”. Thinkleansixsigma, https://www.thinkleansixsigma.com/article/opt-what-is-and-how-it-works. Accessed 23 Jun 2023