What is 5S Methodology
5S Methodology is a workplace organization method that uses a list of five Japanese words: Seiri (Sort), Seiton (Set-in-order), Seisō (Shine), Seiketsu (Standardize), and Shitsuke (Sustain) to organize a workspace for efficiency and effectiveness.
By identifying and storing the items used, maintaining the area and items, and sustaining the new organizational system, 5S helps organizations improve efficiency, avoid wastage, reduce delays, and become competitive.
Simply put, 5S is a systematic approach to workplace organization that leads to reduced costs, increased sales, and a more agile workplace.
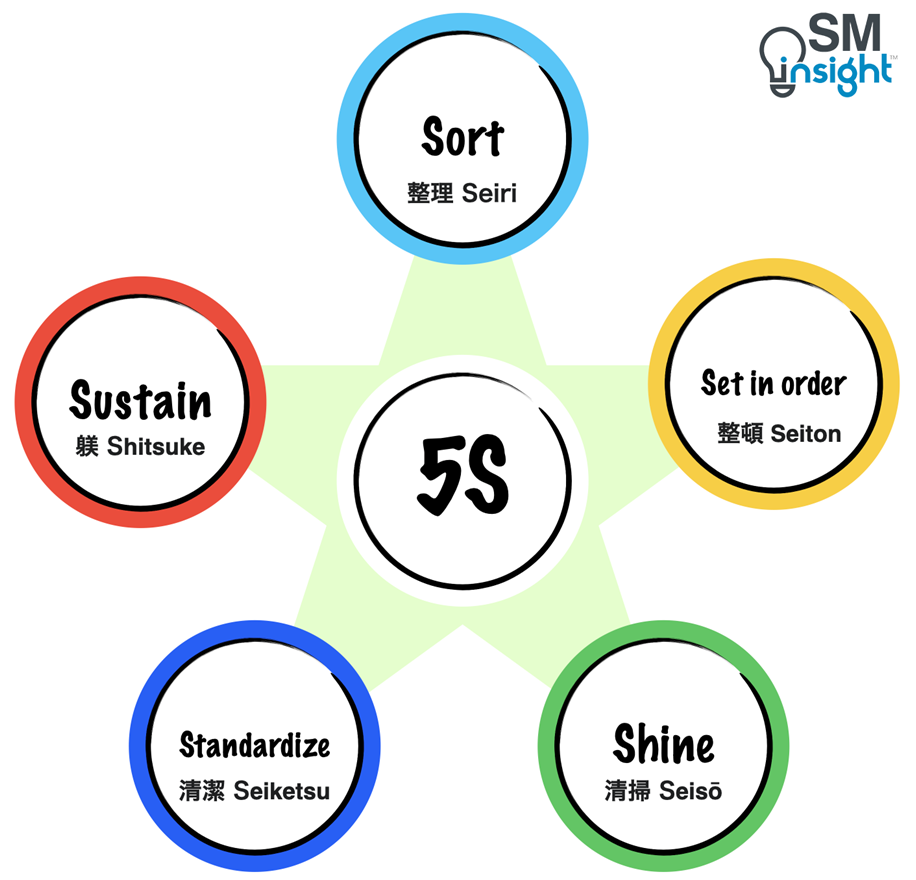
Origin of 5S
In Post-World War II Japan, Toyota’s President, Kiichiro Toyoda and chief engineer Taiichi Ohno visited the U.S. to study the assembly line at Ford and were dismayed by the wastage in manufacturing process.
In contrast, when Kiichiro visited a Piggly Wiggly Supermarket, he was impressed with their system of reordering and restocking as and when goods were purchased.
This inspired them to develop the Just In Time (JIT) manufacturing system at Toyota, the foundations of which lie in 5S. Largely due to Toyota’s success, companies from a variety of industries have since integrated 5S practices into their own processes.
HP, Boeing, Harley-Davidson, Nike, Caterpillar, and Ford are just a few examples that found success with 5S.
Benefits of 5S
Benefit 1: Zero wastage
5S efficiently minimizes waste by eliminating unnecessary storage spaces and reducing “stand-by waste”, such as inventory waiting for equipment. This approach also tackles waste arising from the improper allocation of space and equipment. It even addresses wasteful motion resulting from activities like searching and sidestepping.
The core of the methodology lies in eliminating actions that do not add value, such as the redundant tasks of picking up, putting down, counting, and carrying. With this approach, 5S optimizes processes and enhances overall efficiency.
Benefit 2: Improved Safety
Organizations practising 5S keep their equipment in spotless condition, making mechanical failures and hazards immediately visible. Places are well-defined, and things are stored in designated places. In an industrial setup, this plays a crucial role in eliminating safety incidents and being better prepared in case of an emergency.
Benefit 3: Zero Breakdowns
5S promotes better maintenance by eliminating trash, dirt, and dust which cause equipment breakdowns and shorten life.
By keeping the workspace sparkling clean and free from filings, oil leakage, etc. it becomes easier to monitor equipment condition. Periodic checks built into the 5S keeps breakdowns to a minimum.
Benefit 4: Zero Defects
Defects are harder to discover when the workplace is unorganized. 5S designates a proper place for everything. A clean and well-organized workplace makes workers more conscious of the way they produce things.
Benefit 5: Zero Changeovers
Most factory workers have simply grown accustomed to “searching” as part of their jobs. The more searching they do, the lower their productivity sinks and the more obsolete their factory becomes.
Implementation of the 5S’s makes workshops simple and transparent enough for observers to understand with ease. Proper arrangement of dies, jigs, and tools eliminates this major form of waste called “searching waste.”
Benefit 6: Zero Delays:
When defects are eliminated, deliveries are on time. Good work environments help increase operational efficiency, leading to waste-free workshops.
Benefit 7: Zero Complaints
Products that come from a neat and clean workshop often have no defects, cost less to make and are delivered on time.
Benefit 8: Positive financial impact
Customers are happy to buy from manufacturers that have rid themselves of waste, injuries, breakdowns, and defects. Companies following 5S at workplaces earn more respect and trust in their community and turn competitive.
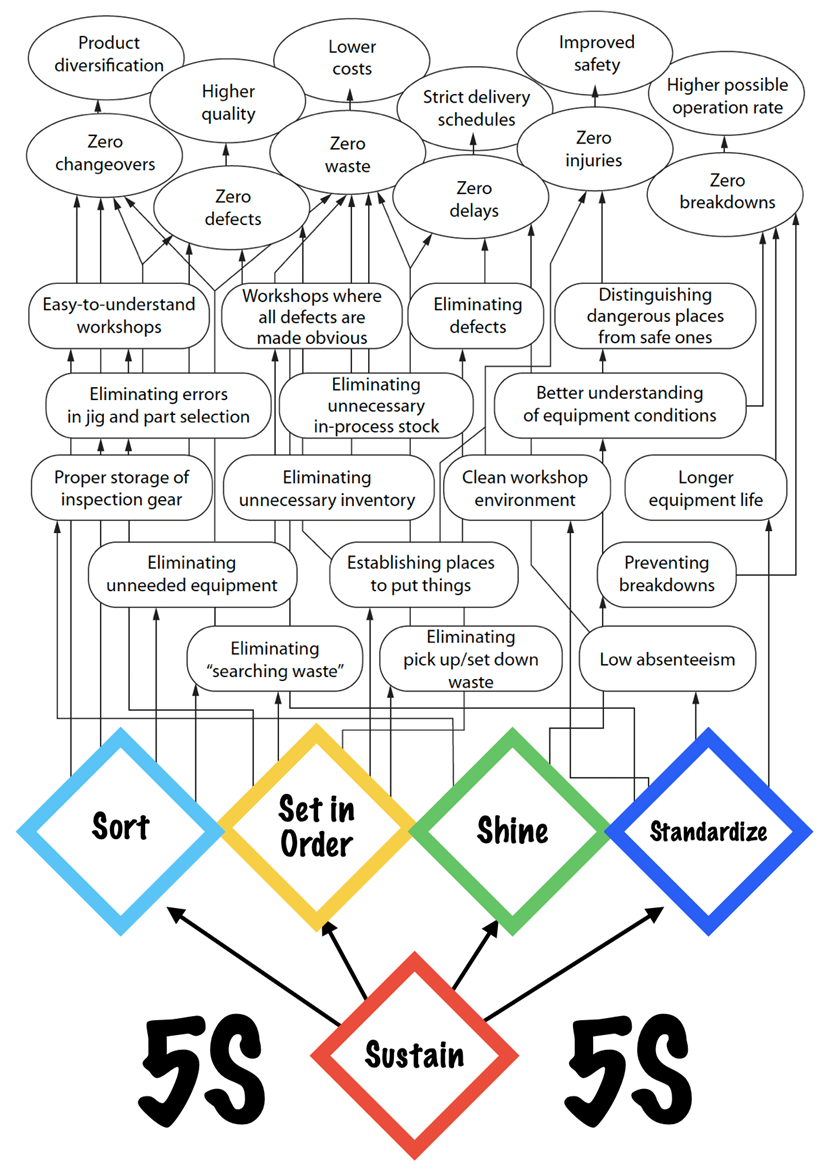
Meaning of the five ‘S’ in 5S
Seiri (Sort)
The word Seiri (to Sort) means proper arrangement and goes beyond lining things up in rows or piling them into neat stacks. It is required to clearly distinguish between what is needed and kept and what is unneeded and thrown out.
Some questions to ask during this phase include:
- What is the purpose of this item?
- When was this item last used?
- How frequently is it used?
- Who uses it?
- Does it need to be here?
Organizations hold onto excess parts, believing they might be of future use. Inappropriate machines are used simply because they are readily available. Eventually, this starts hindering everyday production activities, leading to a mass buildup of waste that spreads far and wide through the factory.
In Seiri, the following types of waste are identified and eliminated:
- Unwanted inventory
- Warehouse space and shelving that do not contribute to the production
- Stocked items that could become obsolete
- In-process inventory
- Equipment that is no longer needed
Visible methods of proper arrangements, such as red-tagging (discussed later), make it easier to identify and eliminate waste.
Seiton (Set in order)
When everything is properly arranged, the only things that remain are the necessary ones. Hence, the next step is to clarify where these things belong. Seiton means to set things in order and goes hand-in-hand with proper management (Seiri).
In this sense, orderliness means designating a place for every item to be kept such that it becomes easier for anyone to find and use.
Things to consider in Seiton include:
- Which people (or workstations) use which items?
- When are items used?
- Which items are used most frequently?
- Should items be grouped by type?
- Where would it be most logical to place items? Would some placements be more ergonomic for workers than others? Would some placements cut down on unnecessary motion?
- Are more storage containers necessary to keep things organized?
During this phase, everyone should determine what arrangements are most logical. This requires thinking through tasks, the frequency of those tasks, the paths people take through the space, etc.
Businesses may want to stop and think about the relationship between the organization and larger Lean efforts. What arrangement will cause the least amount of waste?
One of the key principles of 5S is that anyone must be able to easily understand the order of things in the workspace. This is different from the usual mindset of having to “learn the ropes” or “become a veteran” before understanding where things go.
Seisō (Shine or Clean)
Seisō promotes the practice that cleanliness does not stop at home and that keeping the workplace clean is closely related to the ability to turn out quality products.
Seisō integrates cleanliness into everyday maintenance tasks. By demolishing the distinction between an operator’s work and a maintenance technician’s work, Seisō requires everyone to get involved in maintaining a clean, orderly workspace.
Activities carried out in Seisō include cleaning up the work area, which means sweeping, mopping, dusting, wiping down surfaces, putting tools and materials away, etc.
Seiketsu (Standardize)
Unlike the first three stages, which are seen as activities, Seiketsu refers to a state. Seiketsu means that the first three S’s (Seiri, Seiton, & Seisō) are being maintained.
When a new company implements 5S, it is easy to clean and get organized but gradually, things slide back to the way they were. Seiketsu systematizes the improvements undertaken in the previous three steps and turns these one-time efforts into habits.
By assigning regular tasks, creating schedules, developing standard operating procedures for 5S activities, and posting instructions, Seiketsu ensures that orderliness doesn’t fall by the wayside.
Initially, people will need reminders, and a small amount of time will have to be set aside for 5S tasks, but over time, these tasks become routine and 5S becomes a habit.
Shitsuke (Sustain or Discipline)
Shitsuke is seen as the most important of the 5S’s and is a pivotal factor for the production system as a whole. It is about making 5S a long-term program.
Shitsuke is top-driven, i.e., the seeds of workspace discipline need to be planted by the organization’s bosses and managers by showing their commitment to 5S.
Some of the strategies to drive this step include:
- Audits: managers can take responsibility for maintaining the routines and send a message about their commitment to 5S. Through a coaching attitude, the audit team discusses problems to find long-term solutions.
- Rewards & recognition: Celebrating success is an important part of 5S implementation. Departments and individuals are recognized for their efforts and their successes are displayed for everyone to see.
The goal of Shitsuke is to make 5S a part of an organization’s culture so that businesses achieve continuous positive results.
Implementing 5S
One of the easiest ways to implement 5S is to make the whole array of waste, abnormal operations, and other problems as explicit and visible as possible. This is also referred to as “Visual Management”.
Vision is our dominant sense, and because 5S uses colors, lines, and labels to organize, following the steps becomes second nature very easily. While 5S stands as the foundation for improvement, “visible 5S” is what every 5S initiative must become in order to be preserved.
Numerous process tools can help make 5S successful. Some of them as shown in the figure:
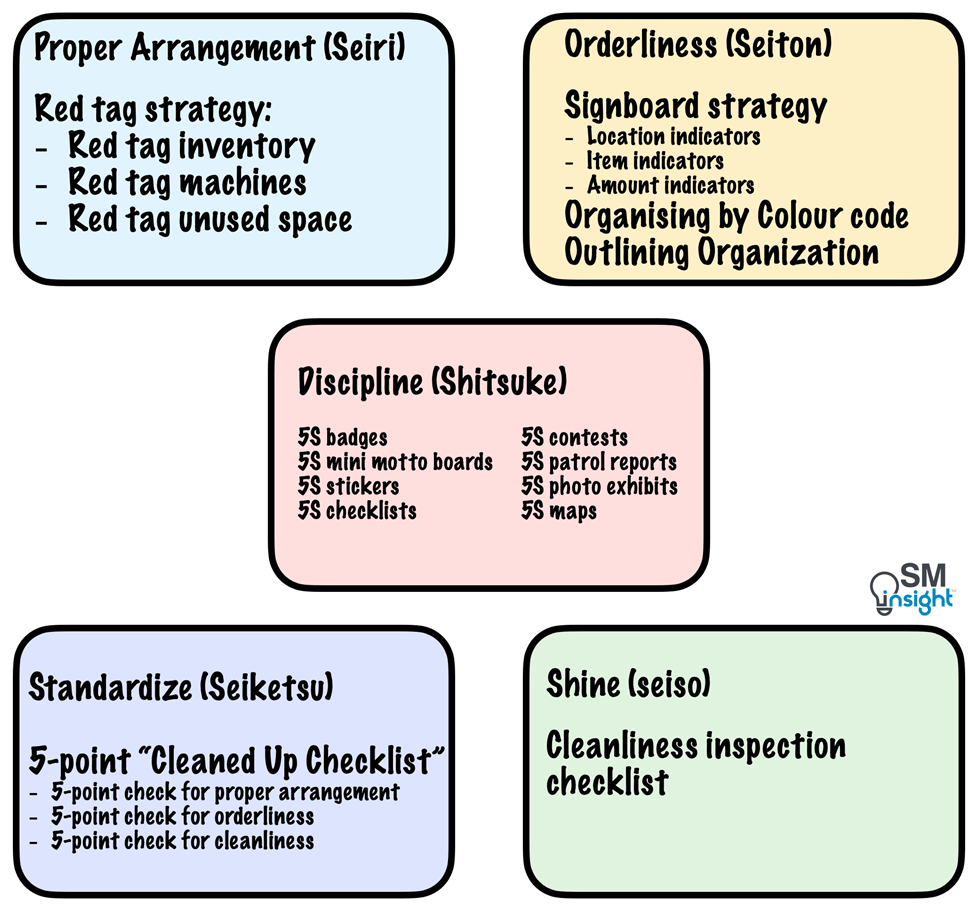
1. Red Tag Strategy
The red tag strategy is a means of implementing proper arrangement by labeling all unneeded items with conspicuous red tags. It involves six steps as follows:
Step 1: Launching the red tag project
Organizations need to carry out factory-wide red tag campaigns at least once or twice a year. A top manager takes responsibility for such a campaign while project members from every division come together in the identification and disposal of unnecessary stock and equipment.
Step2: Identifying Red Tag target area
The main targets for red tags are inventory, equipment, and space. Inventory can be divided into warehouse inventory and in-process inventory.
It is also important to target inventory that does not have a specified location, such as the ones that get piled up alongside aisles or on shelves in the factory. Unnecessary paperwork, along with superfluous desks, lockers etc., also count as target areas in this step.
Step 3: Setting Red Tag Criteria
Organizations are reluctant to throw familiar things away. Establishing well-defined criteria for deciding what is needed and what is not helps address this challenge.
One of the approaches to setting criteria is to look at the 30-day production schedule. What is needed for that schedule is to be retained while the rest could be classified as red-tag items.
Step 4: Make the Red Tags
While organizations can customize the red tags based on their specific needs, at a minimum, the following information is necessary:
- Category (warehouse item, machine, raw materials, in-process inventory etc).
- Item name.
- Quantity indicating the number of items included under the red tag.
- The reason why a red tag is attached (not needed, defective, etc.)
- Responsibility – Department/individual in charge of managing the red-tagged item.
- Date of tagging.
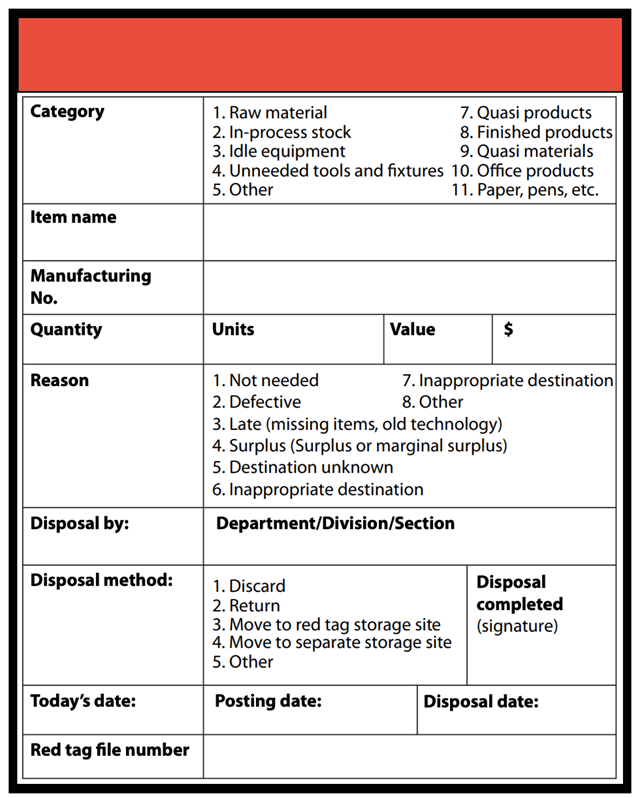
Step 5: Attach the Red Tags
The red-tagging team must thoroughly understand the criteria for selecting the unneeded items. As a good practice, people attaching red tags must not belong to the area being tagged. This ensures that the team is unhindered by sentimental resistance or regret.
The key to a good red-tagging strategy is to cover the whole workspace in as short a time as possible. It is important to regard red-tagging as a swift and powerful event.
Step 6: Evaluate the Red Tag Targets
Red-tagged inventory items can be treated as per the below workflow:
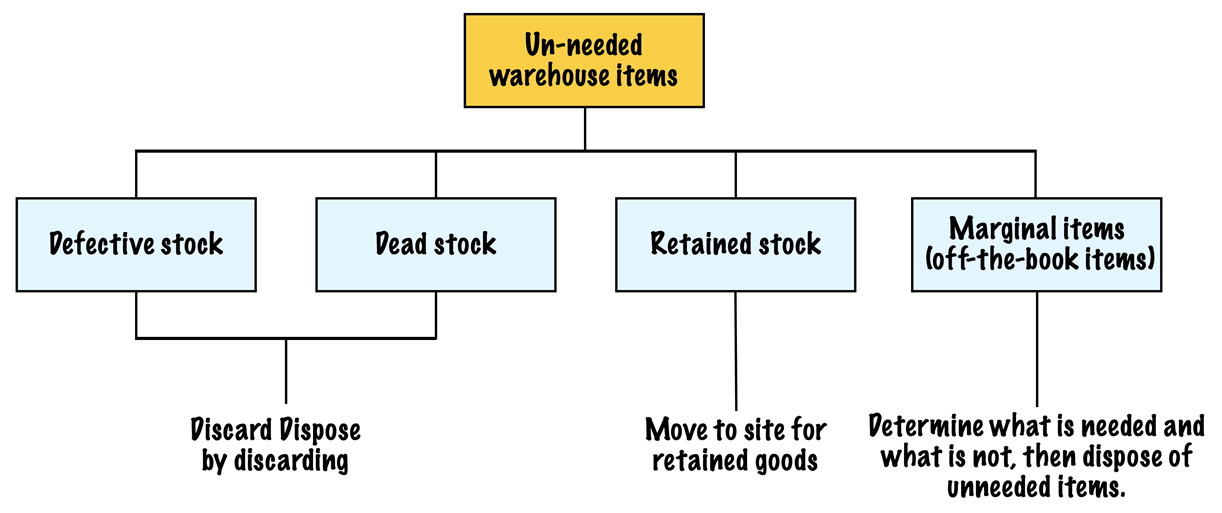
Red-tagging equipment is just as important as warehouse inventory. All such equipment must be moved away from the production area. In case of large equipment that cannot be moved, a “freeze” red tag must be used to indicate that the equipment should not be used for production activities.
2. Signboard Strategy
A signboard strategy is a tool to make the organizing process of 5S more visible. It should always be preceded by the red tag strategy to avoid efforts in posting signboards over unneeded items.
The below figure gives an overview of visible orderliness using the signboard strategy:
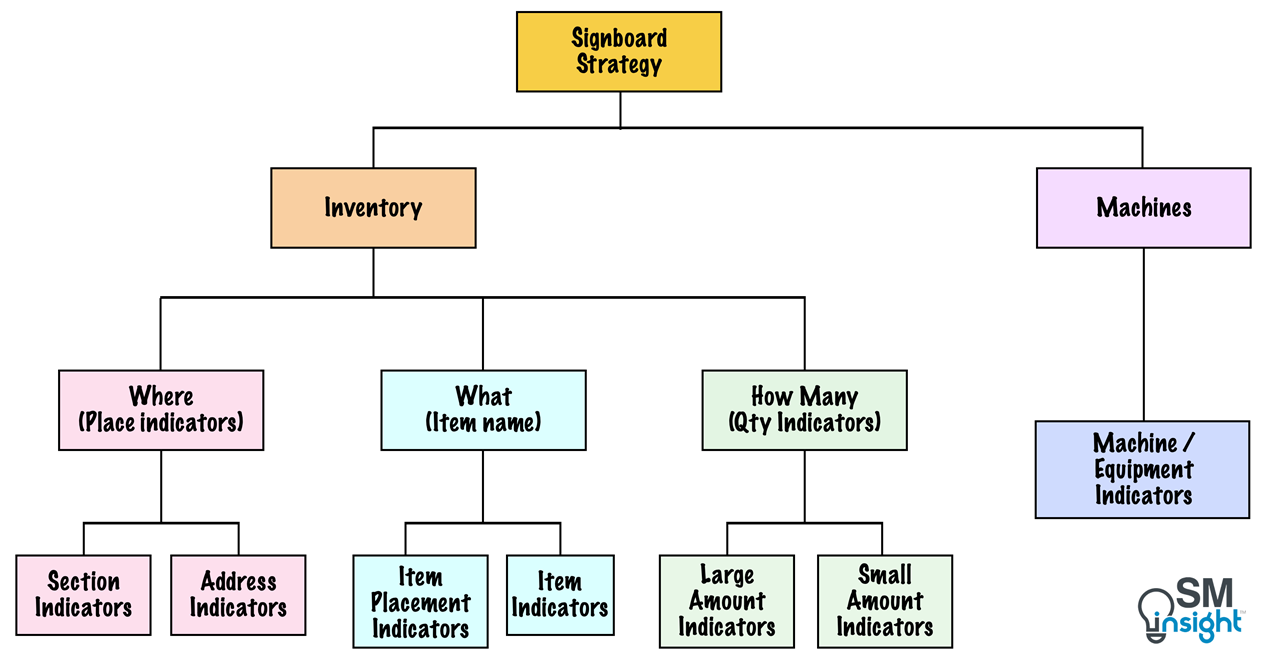
The goal of the signboard strategy is to consolidate what is left after a red-tagging exercise and arrange the equipment layout/production flow pattern in the most efficient and orderly way. It consists of six steps:
Step 1: Determine the locations
To consolidate the equipment layout and the production flow, it is important to determine how things should be placed to best suit the layout. Items that are frequently used must be placed closest to the operator. Ergonomic factors must also be considered in this step.
Step 2. Prepare the Locations
Cabinets, shelving, boxes, pallets, and containers must be used to ensure easy accessibility of storage items (Some of these may be found in red-tagged items and can be repurposed). For better efficiency, First-In First-Out Order[2], or labor-saving roller conveyors may be used.
Step 3: Indicate Locations
Signboards must indicate the place and the address of items. It is essential to indicate where in the factory the item belongs and what specific address in a particular area.
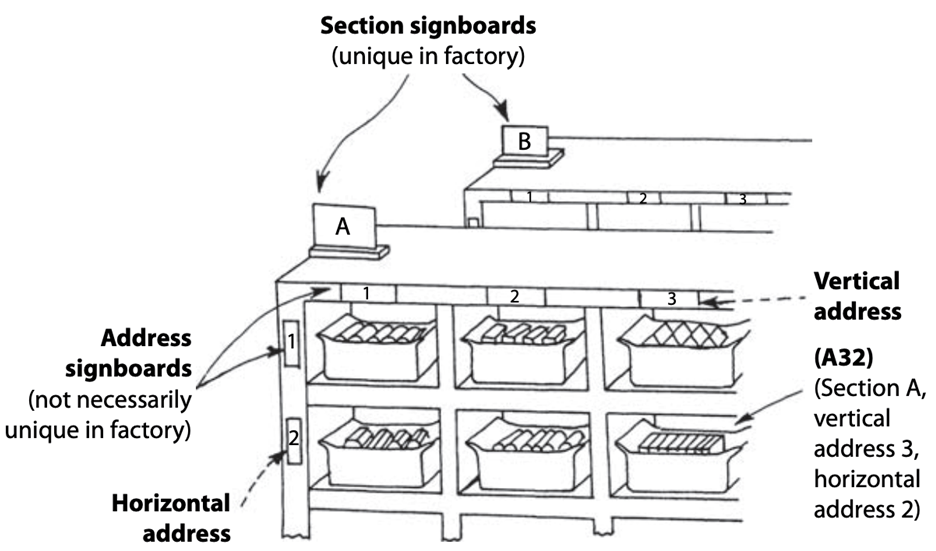
Step 4: Indicate Item Names
While the placement indicators show where the items belong, item indicators identify each item.
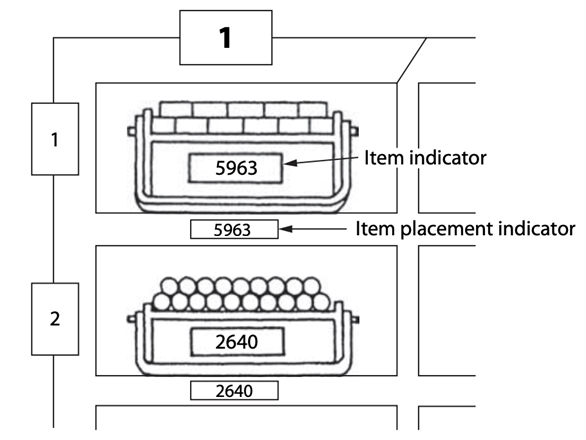
When item indicators include data such as information used to maintain the “pull production” system[3], operation instructions, and/or delivery instructions, these simple signboards turn into a full-fledged Kanban.[4]
Step 5: Indicate Amount
The purpose of amount indicators is to limit the number of shelves and storage space to be used for inventory items. Unless the amount of inventory items is kept under check, they tend to pile up.
When the exact quantity cannot be indicated, the minimum and maximum must be indicated.
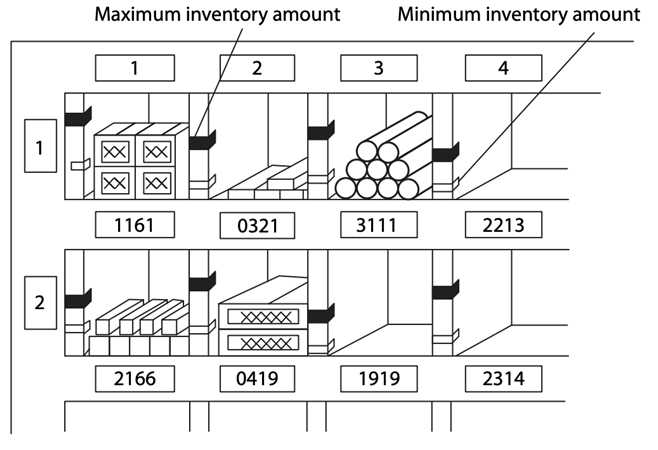
The goal of a good indicator is to help visibly identify abnormalities, waste, and other problems immediately.
Step 6: Maintaining Orderliness
The key to maintaining a successful signboard strategy is to respond to problems as soon as they arise by identifying the causes and making appropriate improvements. Making orderliness easy to maintain, sticking to discipline, and making 5S’s a daily habit is crucial.
3. Organizing by color code
The best way to manage liquids like oil, lubricants, fuel etc. is through color-code. Color-coding the containers and applying the same color-coding to the areas where each type of liquid is stored helps keep the inventory organized.
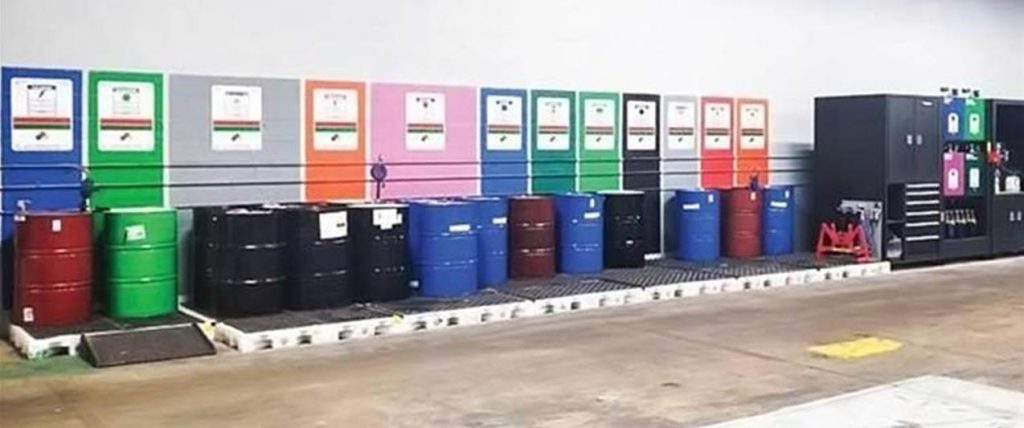
4. Outlining
Marking outlines around the standardized places for keeping things clearly shows anyone where an object belongs. These can be in the form of tapes/paint strips that mark the locations where equipment or materials are placed or highlight hazards.
They come in a variety of colors and patterns, and can also be used on shelves, workbenches, cabinets, and other surfaces.
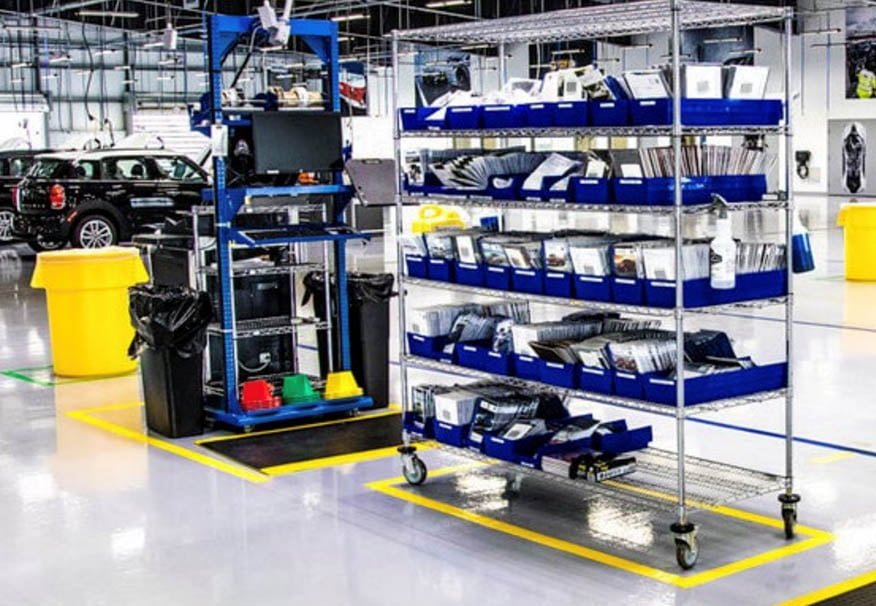
5. Checklists
Checklists provide a structured approach to achieving efficiency and organizing the workplace. They serve as a guide to ensure that each of the five steps in 5S is systematically followed and completed.
Checklists enhance communication, facilitate accountability, and serve as a visual reminder of the tasks at hand.
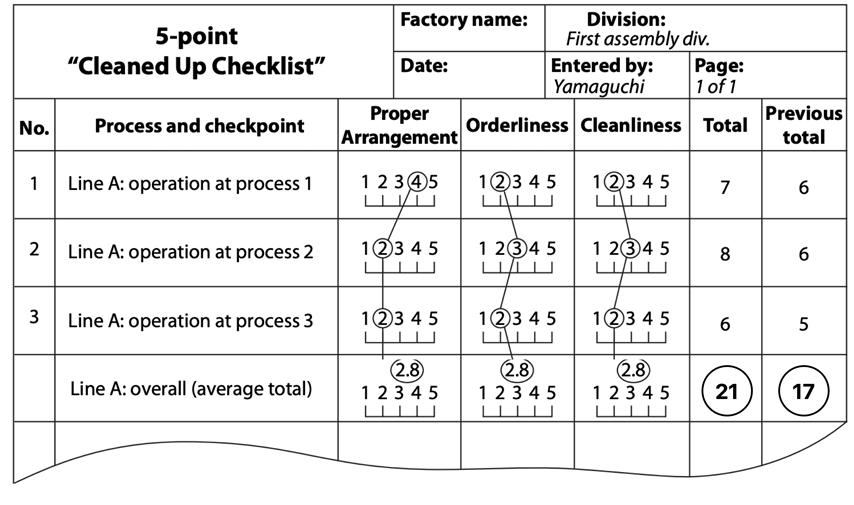
6. Tools for developing discipline in 5S
5S badges
Badges serve as powerful visual reminders of an organization’s dedication to the principles of 5S. They encourage engagement and foster a sense of pride among employees, promoting a culture of organization, cleanliness, and efficiency at the workplace.
5S mini motto boards
Small signboards can be used to post 5S-related mottoes. Such mottoes can be invented by the company’s own workers to heighten awareness and participation. Mottoes & illustrations must be simple enough to be read and understood in under a minute and must be updated frequently.
5S stickers
Stickers act as visual cues to reinforce the principles of 5S. By labeling tools, equipment, and workstations, they remind employees to maintain organization and cleanliness, promoting discipline and adherence to standardized practices in the workplace.
5S contests
5S contests foster discipline by instilling a sense of competition among employees to maintain the best-organized workspace. They encourage individuals and teams to sustain a disciplined approach to organization, cleanliness, and efficiency, ultimately enhancing productivity and overall workplace discipline.
5S patrols
5S patrols contribute to discipline by assigning designated personnel to regularly inspect work areas. Documenting adherence to 5S standards, identifying areas needing improvement, and prompt timely corrective actions helps improve accountability and feedback mechanism.
5S Photo exhibits
5S photo exhibit shows before-and-after images of workspaces, illustrating the impact of implementing 5S principles. These visual representations motivate employees to maintain order, cleanliness, and standardization, fostering a sense of pride and discipline in upholding improved organizational practices.
5S Maps
Maps showcasing factory layouts enable visitors and passersby to easily refer to and identify areas that require better implementation of the 5S’s. Memo pads must be provided alongside maps for taking notes on potential improvements.
Maps help organizations capitalize on collective insights and contributions, fostering a more organized and efficient environment.
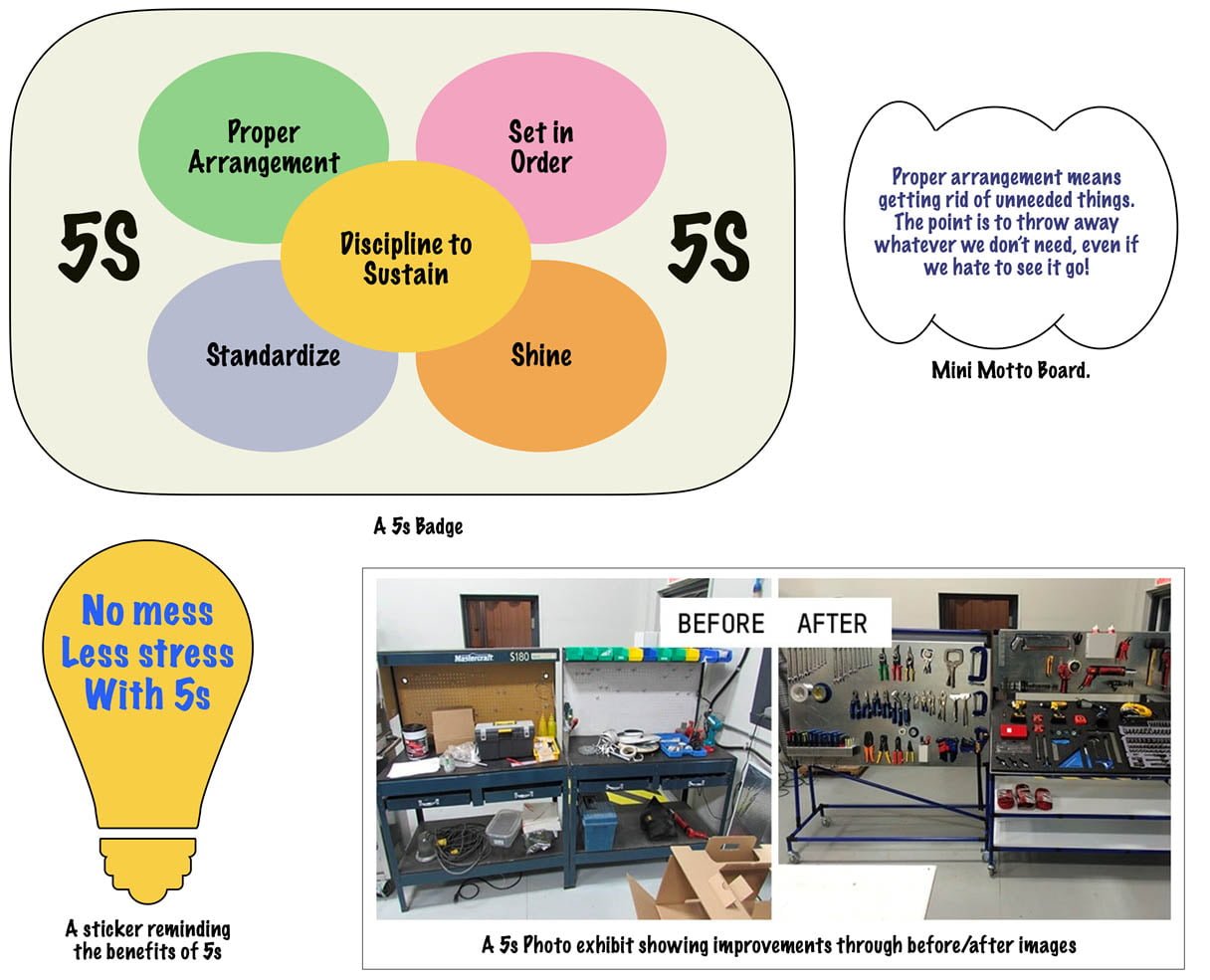
Keys to successful 5S implementation
To ensure the success of any 5S strategy, it is important to organize a “5S Promotion Team”. Such a team is tasked with the responsibility of maintenance and further improvements in 5S.
The following eight points, known as “Eight Keys to 5S Success” are crucial in establishing and maintaining 5S workshops.
Key #1: Getting everyone involved
5S’s cannot be the responsibility of a concerned few. Everyone must get into the act.
All levels of factory management should take part in the decision-making. 5S activities are successful when carried out as a part of the factory’s small-group activities.[7]
Key #2: Get company authorization
Management approval is important in performing 5S activities. A companywide collaborative approach must be followed while avoiding working in isolation.
Key #3: Role of the top management
The 5S’s will not be taken seriously until the CEO/President takes personal responsibility and interest in its implementation. The role of leadership in promoting 5S is crucial.
Key #4: Make everyone understand
Clarity is crucial in 5S. Teams must explain the purpose, method and action plan and address questions from all participants. Using practical examples of successful 5S implementation, including tours of well-maintained workshops, helps bring clarity.
Key #5: Do it all the way
Commitment to 5S is important. Diligent red tag campaigns, clear signboards, well-defined standard operating procedures etc. go a long way in making 5S a success.
Key #6: Top management should drive the initiative
The CEO/president must personally inspect factories and point out their observations. This motivates the group to commit to making the workplace better.
Key #7: Don’t stop halfway in establishing the 5S’s
Once the 5S promotional organization and methods have been established, it is important to follow them all throughout. Developing habits that bring discipline is crucial to keeping the foundation strong.
Key #8: 5S is a continuous improvement process
The act of organizing the workplace, looking for improvements, and optimizing is a continuous process. A successful 5S strategy is one with a shifting goal where there is always room to do better.
Industries using 5s
5S methodology is versatile enough to be used in a variety of industries. Below are some of the industries that have benefited from the 5S methodology.
Industry | Use case |
---|---|
Manufacturing | Toyota pioneered 5s implementation on shop floor and went on to become one of the top automobile manufacturers in the world. |
Medical | Hospitals and pharmacies use 5S to ensure proper labeling, storage, and retrieval to improve overall patient safety. |
Retail | Sorting and organizing practices promoted by 5s is followed by most retail companies to improve efficiency |
Hospitality | Qualities that customers in hospitality expect – order, cleanliness, and consistency are achieved through 5S methodology |
Computers and Technology | Hewlett-Packard’s Computer Systems Division uses 5S to make system building more efficient. 5S concepts are also used to streamline software workflow. |
Education | Classrooms benefit from 5S by eliminating unnecessary items and improving students’ focus and sustaining optimal learning environment. |
Sources
1. “JIT Implementation Manual — The Complete Guide to Just-In-Time Manufacturing: Volume 2 — Waste and the 5S’s 2nd Edition”. Hiroyuki Hirano, https://www.amazon.com/Implementation-Manual-Complete-Guide-Manufacturing/dp/1420090240. Accessed 16 Jul 2023
2. “FIFO – First In First Out Warehousing”. Ogiwa, https://www.logiwa.com/blog/first-in-first-out-warehousing. Accessed 18 Sep 2023
3. “Pull Production”. Lean.org, https://www.lean.org/lexicon-terms/pull-production/. Accessed 19 Jul 2023
4. “What Is the Kanban System?”. Investopedia, https://www.investopedia.com/terms/k/kanban.asp. Accessed 18 Jul 2023
5. “World-class Lubrication Program Transformation”. Machinerylubrication.com, https://www.machinerylubrication.com/Read/881/world-class-lubrication. Accessed 18 Jul 2023
6. “5s Guide”. Creative Safety Supply, https://www.creativesafetysupply.com/content/landing/5S-poster/index.html. Accessed 18 Jul 2023
7. “Small Group Activity – SGA”. Makigami, https://www.makigami.info/continuous-improvement-tools/small-group-activity-sga/. Accessed 19 Jul 2023